Realizzazione della produzione a circuito chiuso
Integrazione di ERP, PLM e MES per realizzare la Smart Manufacturing
Introduzione
La digitalizzazione sta cambiando il modo in cui gli esseri umani vivono e si comportano sotto molti punti di vista e ha un impatto enorme in quasi tutti gli ambiti della società. Basta guardare la produzione: le fabbriche utilizzano applicazioni digitali da decenni, ma l'impatto di un nuovo paradigma tecnologico fondato sull'Industrial Internet of Things (IIoT) e realizzato nel concetto di Industria 4.0, sta spingendo il mondo della produzione verso un campo da gioco completamente diverso.
Entra nella Smart Manufacturing (produzione intelligente), dove nuove prospettive consentono alle strategie di produzione di evolversi così da promuovere l'ottimizzazione dei processi, il supporto decisionale intelligente e il miglioramento continuo di prodotti, processi e persone.
Ma come è possibile raggiungere questo obiettivo? Semplice: con informazioni e connettività. I dati sono la chiave e l'integrazione, in senso lato, è lo strumento che consente la produzione intelligente.
E chi sono gli attori? Aziende, clienti, partner, fornitori e distributori devono essere considerati gli attori chiave della moderna supply chain, nella quale la generazione, l'utilizzo e la condivisione dei dati funge da base per processi efficienti e creazione di valore.
Perché l’integrazione? L'integrazione delle applicazioni digitali consente la condivisione efficace dei dati. Un modo efficiente di elaborare e analizzare i dati può generare elementi di conoscenza informati che tengono conto di ogni fase del ciclo di vita del prodotto. Con le informazioni corrette, tutte le funzioni dell'azienda diventano più sostenibili, più efficienti, più proattive e, soprattutto, più capaci di generare valore per il business.
Seguendo questo approccio di integrazione, è possibile creare un unico processo continuo, chiamato produzione a circuito chiuso, comprendente pianificazione aziendale, progettazione del prodotto, pianificazione ed esecuzione della produzione ed infine consegna del prodotto.
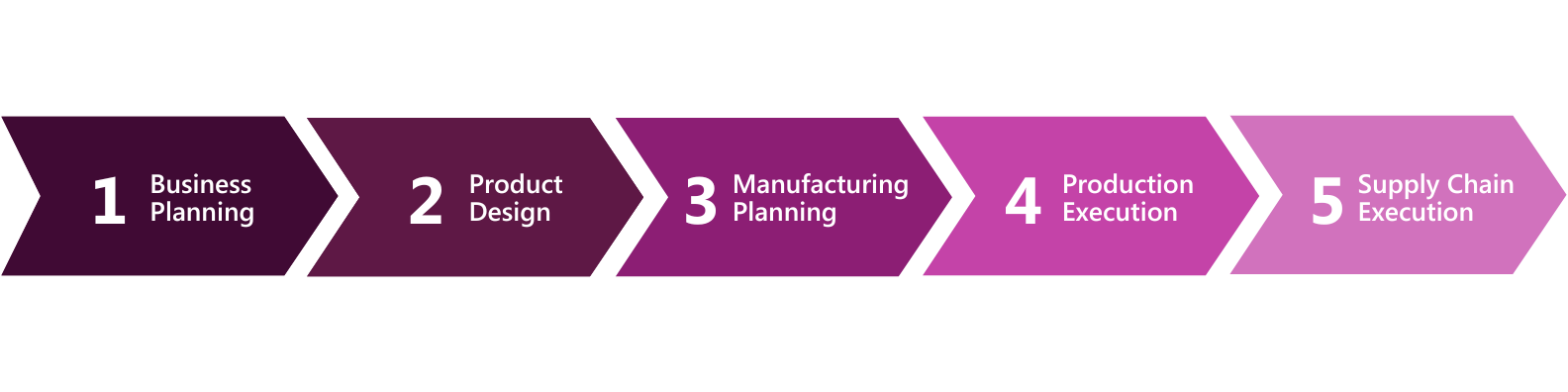
La proposta
Tenendo conto di questi concetti, il Gruppo Engineering ha combinato le potenzialità della propria competenza nei processi aziendali, esperienza intersettoriale e conoscenza tecnica approfondita delle migliori applicazioni industriali sul mercato, per offrire una visione per la produzione intelligente che oggigiorno può essere effettivamente realizzata.
In termini software, quando Product Lifecycle Management (progettazione del prodotto e pianificazione della produzione), Manufacturing Execution Systems (esecuzione della produzione e controllo qualità) e Enterprise Resource Planning (pianificazione aziendale, gestione intelligente degli asset e fornitura del prodotto) si uniscono, la somma, come accade a volte, diventa maggiore di ognuna delle sue singole parti.
In termini di integrazione, i centri di competenza globali del Gruppo Engineering offrono le capacità critiche necessarie per colmare il divario digitale tra business, ingegneria e operazioni. I nostri team Engineering Industries eXcellence ed Engineering Enterprise Solutions vantano un’approfondita esperienza e dispongono delle risorse qualificate necessarie per progettare, implementare e integrare processi e tecnologie in PLM, MES ed ERP al fine di garantire un approccio integrato che consenta alle aziende di produzione in tutti i settori industriali di tutto il mondo di implementare le loro visioni di produzione intelligente.
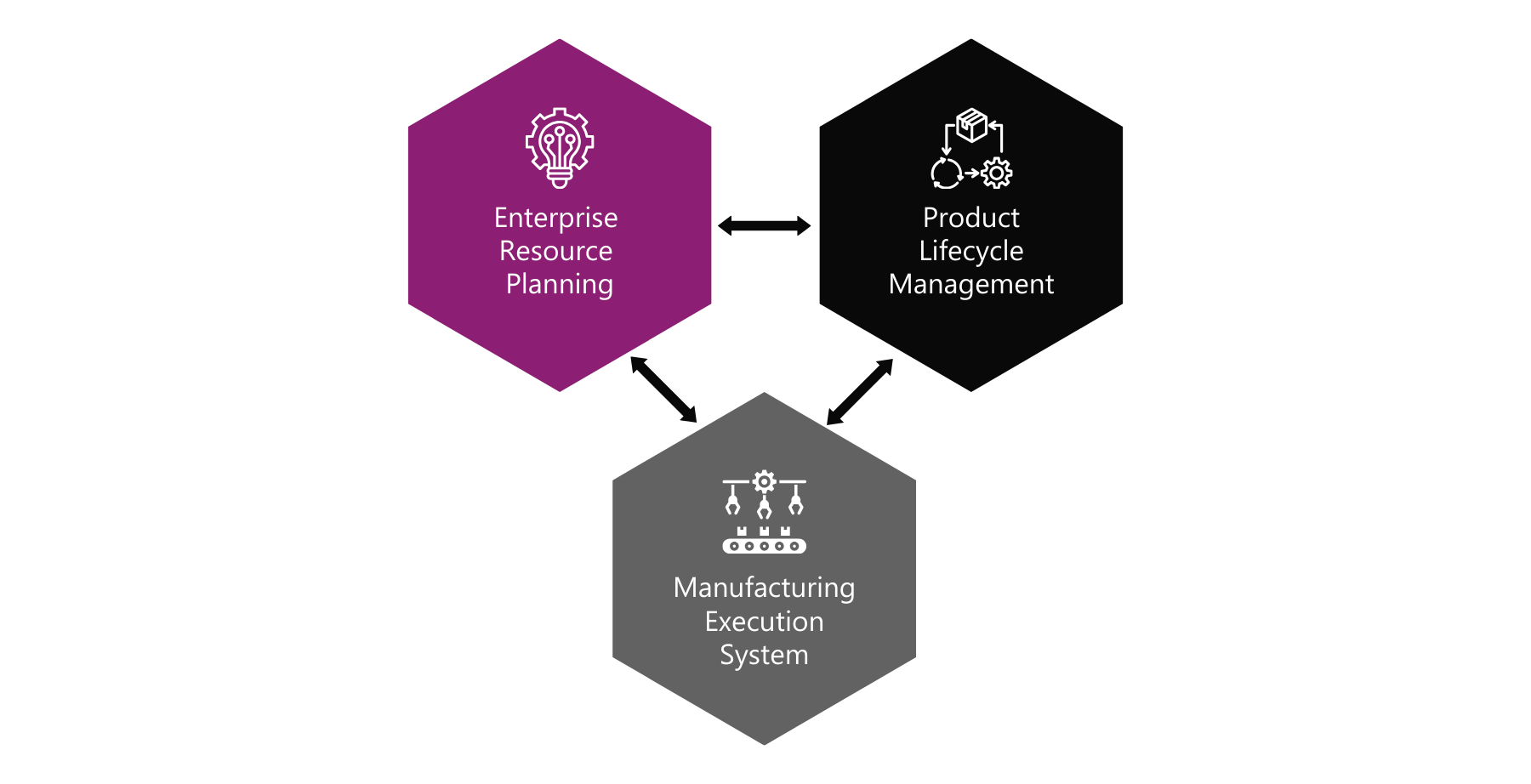
I requisiti aziendali
La produzione intelligente consente una produzione sostenibile ed efficiente per natura. Il requisito fondamentale, in ogni singola fase del processo di produzione, è che siano disponibili tutte le informazioni del caso, così da poter prendere la decisione giusta o attivare automaticamente la procedura giusta. I dati che costituiscono queste informazioni possono essere generati in molti luoghi e in molti modi diversi.
Progettazioni di prodotti, apparecchiature di produzione, sistemi di test di produzione e persino i beni prodotti sono tutte fonti dei cosiddetti dati front-end. Questi dati sono gestiti tramite PLM, MES e relative applicazioni operative.
Al tempo tesso, i dati back-end, che vengono gestiti tramite ERP e le relative applicazioni aziendali, sono similmente una fonte di informazioni molto rilevante e importante che impatta sulla produzione. Esempi di questi dati includono richieste dei clienti, ordini di vendita, disponibilità di ricambi, piani di manutenzione, piani di turni del personale e così via.
Anche i dati della catena di fornitura provenienti da entità esterne quali partner, fornitori e distributori devono essere parte integrante del quadro, in quanto forniscono i ricambi e i servizi necessari per l'esecuzione dei processi di produzione e consegna. Anche le informazioni di logistica e di gestione dei materiali provenienti dai magazzini dei prodotti e dalle reti di trasporto hanno un ruolo rilevante.
Inoltre, non vanno dimenticati i dati di mercato relativi alla domanda, agli aspetti economici/finanziari, alla disponibilità delle scorte, alle esigenze di rifornimento, alle linee guida normative e molto altro ancora.
Pensandoci bene, tutti questi dati sembrano non finire mai. Per consentire una gestione operativa efficace, questa enorme mole di dati deve prima essere raccolta, analizzata e presentata in modo tempestivo, accurato e corretto. E per consentire una vera produzione intelligente, l'intelligenza artificiale e l'apprendimento automatico devono poi essere applicati per guidare costantemente un processo decisionale maggiormente ottimizzato, intelligente e in ultima analisi autonomo.
I processi supportati
Comprendere e sfruttare le potenzialità dei dati è fondamentale per la produzione intelligente, ma non è sufficiente. In che modo tutte queste diverse fonti di dati interagiscono e incidono l'una sull'altra? È necessario capirlo al fine di creare un piano di integrazione fattibile che colleghi con successo tutti i diversi processi che interagiscono con la produzione nell’intera organizzazione. Quando il ciclo è chiuso e i dati sono disponibili nella forma giusta, la produzione è efficiente e la qualità migliora.
Prendiamo ad esempio il settore della produzione di alimenti e bevande. Quali sono i processi interessati? Quali sono i gruppi aziendali e i reparti coinvolti? Come interagiscono con la produzione? Qual è l’impatto che la produzione ha su di essi?
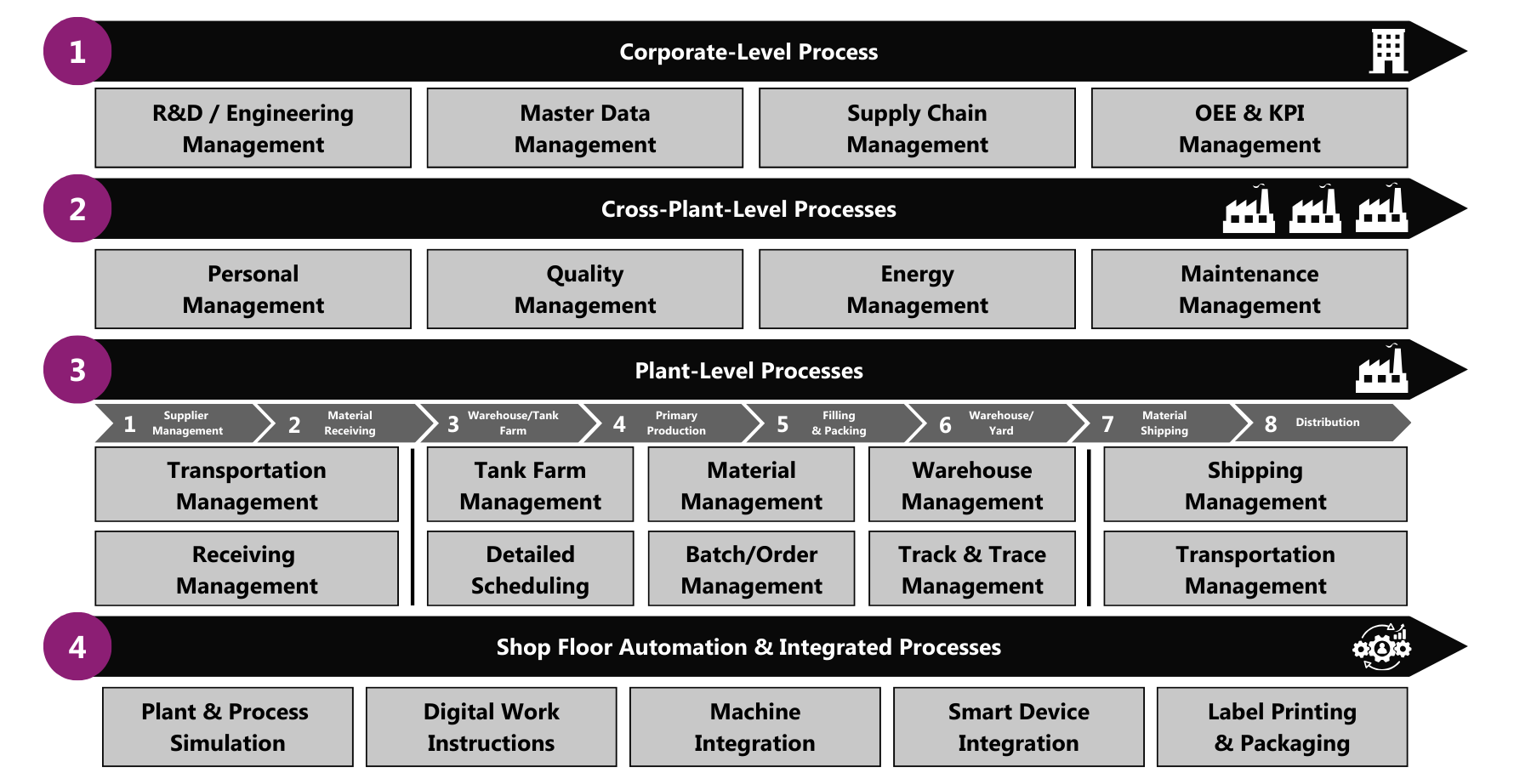
Livello 1: processi a livello aziendale
A livello aziendale, esiste una serie di processi comuni a tutta l'impresa organizzativa. Sono integrati verticalmente e comunicati fino a raggiungere l'apparecchiatura in fabbrica.
Ad esempio, le modifiche nella progettazione del prodotto da parte dell’ingegneria vengono trasferite a valle e all’intera azienda, determinando modifiche nella pianificazione, approvvigionamento, operazioni e, in ultima analisi, nel modo in cui il prodotto viene realizzato in fabbrica.
Livello 2: processi tra più stabilimenti
A livello dei diversi stabilimenti, esiste una serie di processi che devono essere gestiti e valutati nel loro complesso, per tutte le funzioni e attività aziendali, di solito perché vi è una forte esigenza di standardizzazione tra stabilimenti.
Ad esempio, per confrontare l'efficienza dei diversi siti, le aziende devono definire come misurare gli indicatori chiave di prestazione in modo standardizzato – in termini di Overall Equipment Effectiveness (OEE), volumi di produzione, utilizzo delle risorse, consumo di energia, ecc.
Livello 3: processi a livello di stabilimento
A livello di fabbrica esiste una serie di processi la cui pianificazione di alto livello viene avviata a livello aziendale, quindi trasferita a valle a tutte le operazioni e infine implementata dettagliatamente nel singolo stabilimento.
Ad esempio, gli ordini generati dalle vendite per soddisfare una nuova domanda o richiesta del cliente saranno programmati per essere prodotti in un'area, un impianto o una linea specifica in base a vincoli, requisiti e priorità diversi.
Livello 4: processi integrati nell'area produttiva
L’integrazione di processi e asset dell'area produttiva nel flusso di lavoro di produzione intelligente consente l'ottimizzazione e il miglioramento continui delle attività mentre vengono eseguite da persone e macchine nel reparto di produzione.
Ad esempio, l'integrazione di dispositivi intelligenti per il monitoraggio delle prestazioni degli asset consente ai responsabili di stabilimento di supervisionare la produzione in tempo reale. Di conseguenza, è possibile reagire più rapidamente a eventi imprevisti e quindi prevenire costose interruzioni.
L’architettura tecnica
Per consentire la produzione intelligente attraverso flussi di dati a circuito chiuso, la chiave è realizzare l'integrazione di PLM, MES ed ERP tramite interfacce tecniche bidirezionali. I tre sistemi, una volta integrati, diventano interdipendenti e la conseguente architettura tecnica è in grado di supportare l'intero processo del ciclo di vita del prodotto dall'inizio alla fine:
- Product Lifecycle Management (PLM) offre funzionalità di gestione dei dati per la progettazione e la definizione del prodotto, la pianificazione della qualità e del processo di produzione, la configurazione del prodotto e la gestione delle modifiche;
- Manufacturing Execution Systems (MES) offrono capacità di esecuzione operativa per l'esecuzione degli ordini di produzione, la raccolta dei dati sulla produzione e la qualità, i test di qualità e la conferma della produzione;
- Enterprise Resource Planning (ERP) offre capacità aziendali di alto livello per la pianificazione delle vendite, le operazioni della catena di fornitura, la pianificazione della produzione, l'approvvigionamento, la gestione intelligente degli asset e delle risorse in tutta l'azienda.
L'obiettivo dell'integrazione è implementare il Digital Thread, un flusso di dati senza soluzione di continuità che garantisce la disponibilità di tutte le informazioni corrette quando e dove necessario. L'architettura tecnica risultante diventa quindi la base dei modelli di processo aziendale dell'organizzazione per la produzione a circuito chiuso.
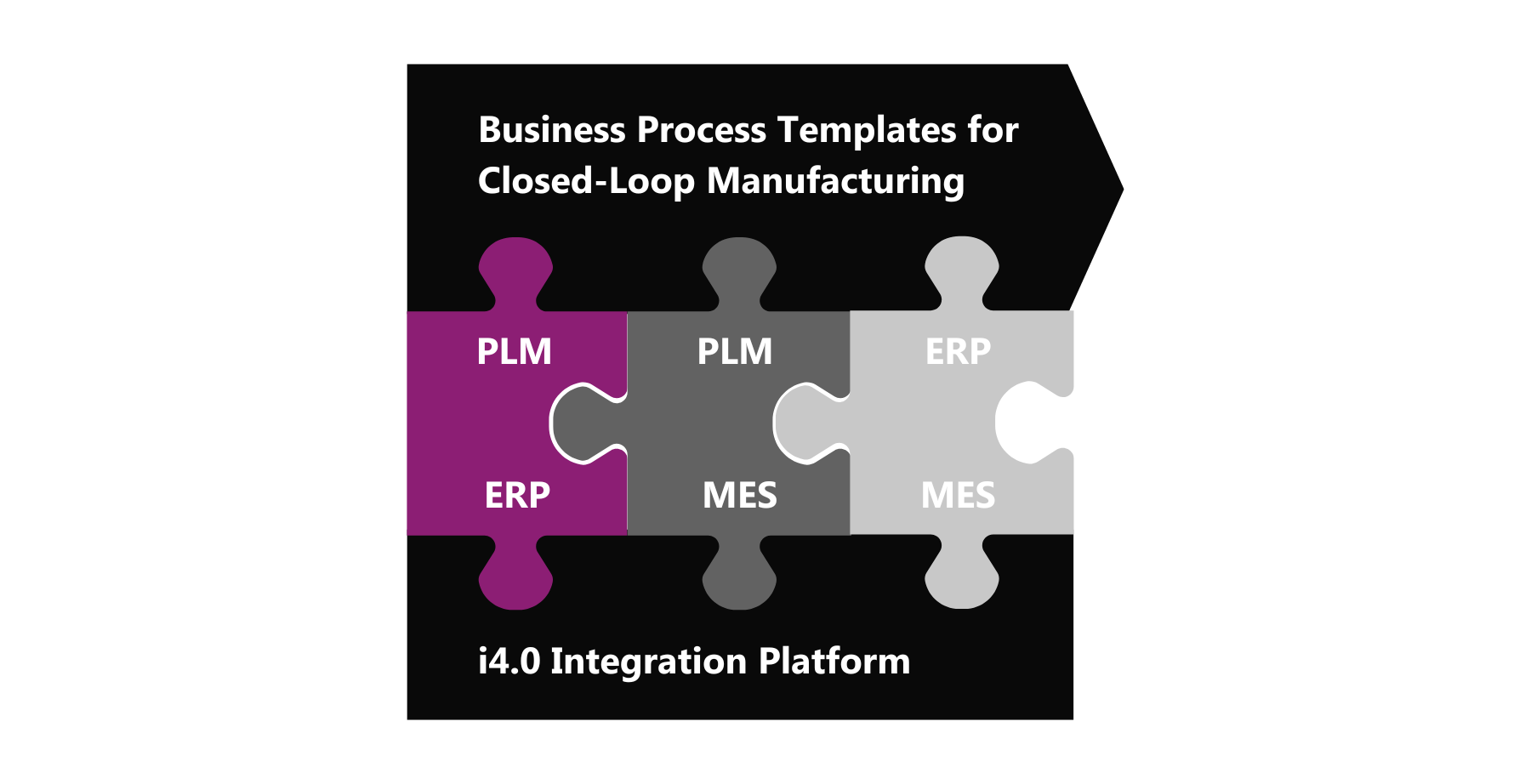
Interfaccia: integrazione ERP e PLM
La prima interfaccia bidirezionale implementata permette il collegamento collaborativo tra PLM ed ERP, garantendo così che il sistema di registrazione per il prodotto in PLM alimenti il sistema di registrazione per la pianificazione aziendale in ERP. Il sistema PLM gestisce i dati di prodotto a partire dalla progettazione iniziale, non appena viene rivista e attraverso il rilascio per la produzione, mentre il sistema ERP utilizza la verità di prodotto fornita da PLM per pianificare e gestire accuratamente le risorse produttive e finanziarie. Questa sincronizzazione tramite integrazione è la chiave per promuovere lo sviluppo di prodotti innovativi e la redditività del loro lancio commerciale.
Interfaccia: integrazione PLM e MES
La seconda interfaccia bidirezionale implementata permette il collegamento collaborativo tra PLM e MES, estendendo così il valore delle ampie funzionalità di gestione dei dati di un sistema PLM dalla progettazione e pianificazione della produzione all'esecuzione del flusso di lavoro della produzione. Questa integrazione crea una single source of truth per tutto il ciclo di vita del prodotto, garantendo che ogni ordine evaso in fabbrica sia in linea con tutte le specifiche di prodotto e di processo. In questo modo la qualità è controllata e garantita, il rischio di costose rilavorazioni eliminato e il time-to-market significativamente ridotto.
Interfaccia: integrazione ERP e MES
La terza interfaccia bidirezionale implementata permette il collegamento collaborativo tra ERP e MES, garantendo il pieno allineamento tra le funzioni di pianificazione aziendale e di produzione dell'azienda. Questa integrazione consente lo scambio tempestivo di informazioni critiche tra le vendite, gli acquisti e le reti di fornitori con le attività in tempo reale nell'area produttiva. I dati condivisi e sincronizzati attraverso tale integrazione possono includere lo stato e la disponibilità di materie prime, magazzini, giacenze di prodotti, persone, asset, attrezzature e dati.
Connessione: piattaforma di integrazione i4.0
Tutte e tre le interfacce tecniche bidirezionali sono collegate alla piattaforma di integrazione i4.0, un hub centralizzato basato su cloud che offre tutti i servizi necessari per realizzare e gestire le interconnessioni e le interfacce multisistema. La piattaforma flessibile è progettata e costruita in modo da offrire alle aziende di produzione la possibilità di estendere le proprie capacità da e verso altri sistemi o applicazioni aziendali, se e quando lo si desidera.
Progettazione della soluzione
Trasformazione digitale significa utilizzare la tecnologia per creare nuovi processi aziendali, o modificare quelli esistenti, e adattarsi all’evoluzione delle esigenze del mercato. Una strategia di digitalizzazione efficace comincia con una valutazione approfondita dei processi “AS-IS” di un'azienda, i cui risultati determinano poi la progettazione di una soluzione “TO-BE” olistica, in grado di soddisfare tutte le esigenze funzionali e aziendali.
Cosa: mappatura dei processi e modelli
Per aiutare le aziende industriali a controllare e integrare tutti i flussi di informazioni che interagiscono con la produzione, è stata definita una serie comprovata di modelli specifici per settore e metodologie di best practice. Questi vengono utilizzati per documentare i processi, sia manuali sia automatizzati, tra i diversi reparti dell'azienda così da creare una mappa visiva di come interagiscono tra loro e con le operazioni in fabbrica. Utilizzando questa roadmap, è possibile garantire che nessun processo venga dimenticato nella progettazione della soluzione finale.
Chi: progettazione dell'applicazione basata sui ruoli
Fin dall’inizio nella strategia di digitalizzazione è necessario considerare e integrare anche il ruolo delle persone. Come si può essere certi di offrire un valore incentrato sugli utenti? Come è possibile garantire che l'infrastruttura digitale sia costruita in modo tale da supportare le persone e il loro continuo miglioramento? È possibile farlo raccogliendo i requisiti degli utenti all'inizio e collaborando con loro e con gli altri portatori d'interesse durante tutto il processo di sviluppo.
Come: approccio alla digitalizzazione bimodale
I nostri modelli dei processi aziendali specifici per settore sono stati creati per coniugare un'evoluzione maggiormente prevedibile di prodotti e tecnologie standard con i più recenti e innovativi approcci alla digitalizzazione. Questa è l'essenza di quello che Gartner ha definito l'approccio alla digitalizzazione bimodale a due velocità.
Se implementato correttamente, questo approccio alla progettazione di soluzioni favorisce il percorso più rapido ed efficace verso la produzione intelligente per le aziende industriali di tutti i settori. L'approccio a due velocità prevede che la roadmap per l'Industria 4.0 di un'azienda debba considerare e includere due architetture di soluzioni separate (ma contemporanee e complementari):
- Modalità 1 incentrata su PREVEDIBILITÀ e AFFIDABILITÀ (ad esempio, sistemi di base come ERP, PLM, MES, QMS, ecc.);
- Modalità 2 incentrata su AGILITÀ ed ESPLORAZIONE (ad esempio, tecnologie abilitanti – Cloud, Low Code, AI, ecc.).
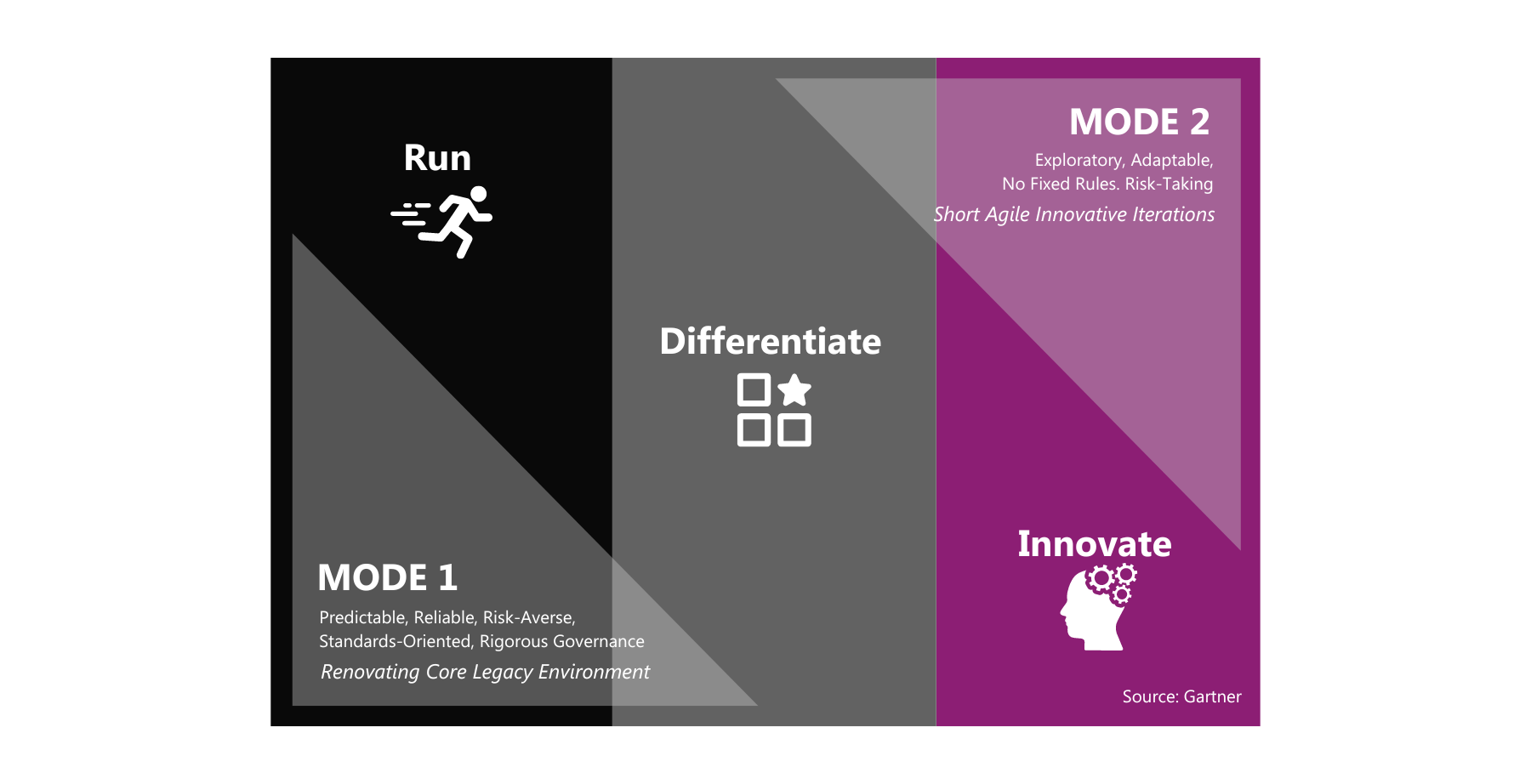
Creazione della soluzione
Ogni segmento del blueprint della soluzione progettato è sviluppato e convalidato seguendo la metodologia proprietaria di implementazione del software della nostra organizzazione: ENGILE.
ENGILE combina un approccio agile innovativo con elementi specifici della metodologia tradizionale a cascata per lo sviluppo di software. Di conseguenza, non solo siamo in grado di fornire soluzioni di produzione a circuito chiuso integrate in modo più rapido ed economico rispetto a qualsiasi altro integratore di sistemi al mondo, ma lo facciamo garantendo anche la massima qualità.
L'approccio ENGILE ha dimostrato di ridurre al minimo i rischi, aumentare il controllo e raggiungere gli obiettivi del progetto nei tempi e nei modi previsti.
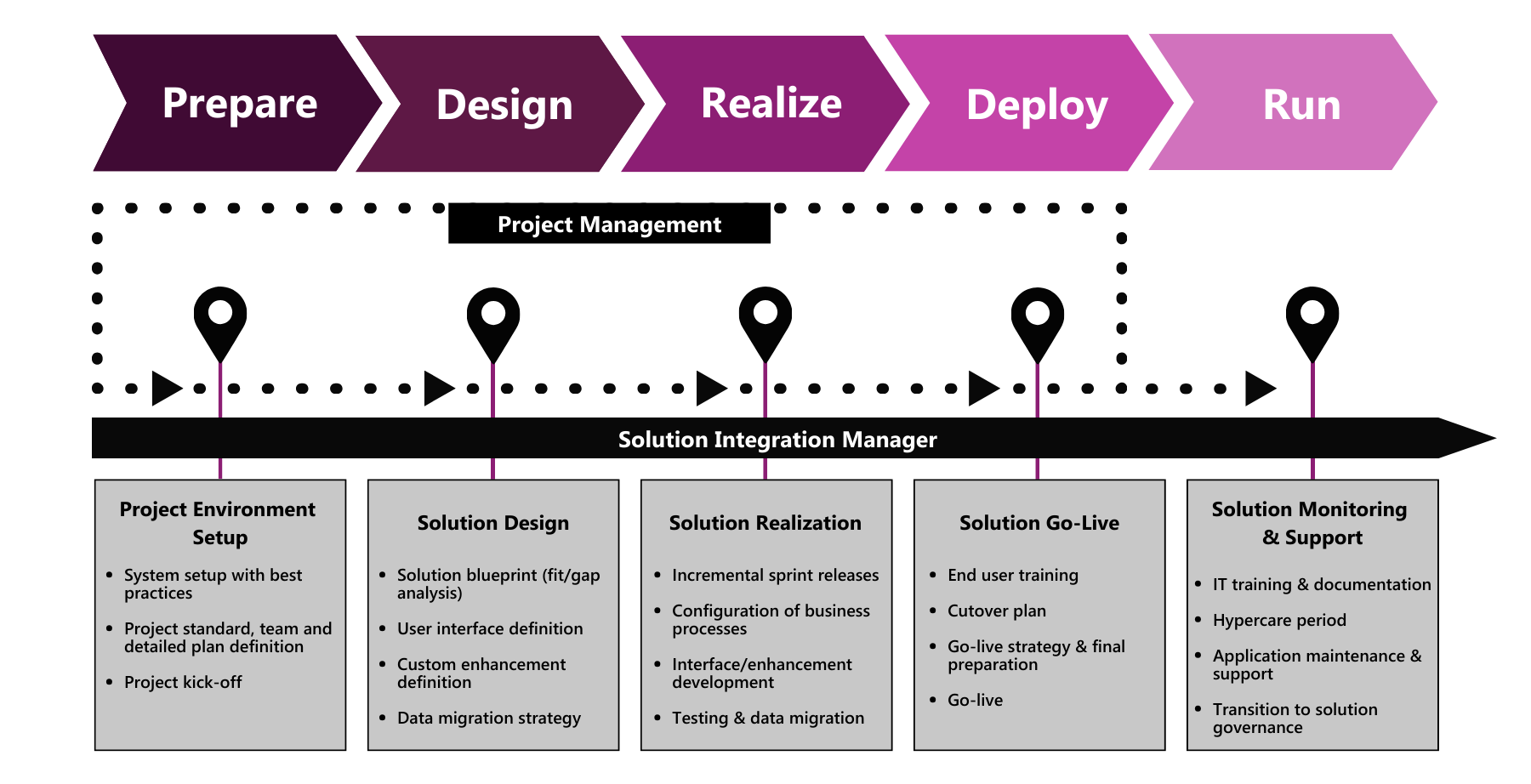
Fornitura del progetto
Il nostro approccio tipico per fornire con successo un progetto di produzione a circuito chiuso inizia con un progetto pilota o proof-of-concept, seguito da tre fasi di implementazione:
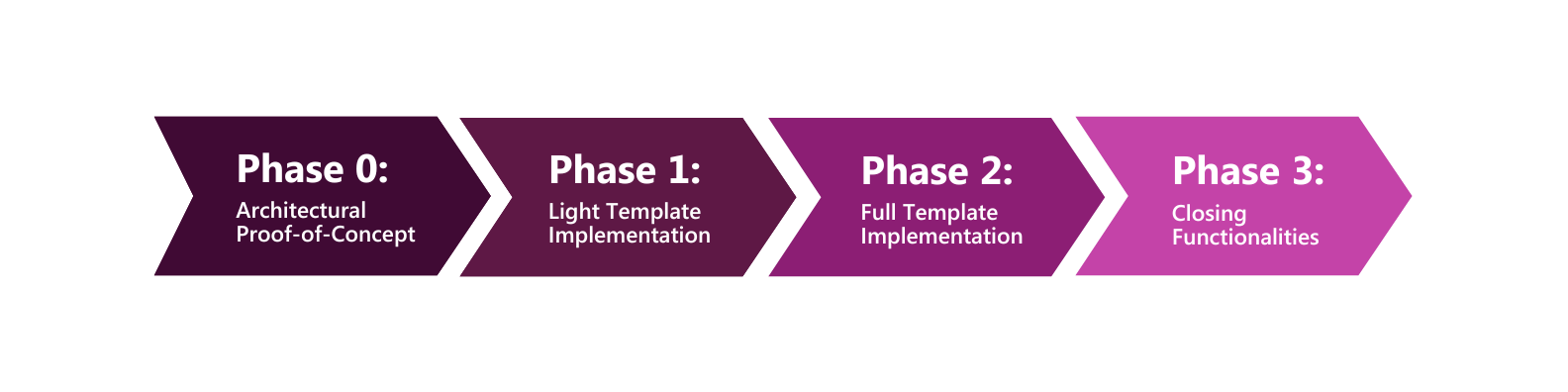
Fase 0: proof-of-concept
Il proof-of-concept mira a testare funzioni e capacità selezionate della soluzione finale in uno stabilimento o su una linea di produzione selezionati, al fine di garantire la fattibilità della soluzione senza rischiare di interrompere le attività della fabbrica stessa o le operazioni aziendali. Questo è anche il punto di partenza per la progettazione dell'ambiente della piattaforma di integrazione i4.0 su cloud, tenendo in considerazione la connettività con le interfacce tecniche bidirezionali da definirsi nella fase successiva.
Fase 1: implementazione del modello "light"
L'implementazione del modello "light" intende estendere il proof-of-concept così da coinvolgere un maggior numero di stabilimenti e/o linee di produzione. Include anche l'implementazione della prima versione dell'architettura di integrazione, realizzando una connessione tra le interfacce bidirezionali e la piattaforma di integrazione i4.0 e convalidando le funzionalità critiche di raccolta e gestione dei dati.
Fase 2: implementazione del modello completa
L'implementazione del modello completa permette di attivare tutte le restanti funzionalità della soluzione integrata di ERP, PLM e MES come progettato. Questa fase prevede attività che personalizzano le funzionalità della piattaforma di integrazione i4.0 su cloud. Possono anche essere installati server locali, tutti integrati con la piattaforma, per consentire un maggiore controllo in loco.
Fase 3: definizione delle funzionalità
La fase di definizione delle funzionalità intende completare la realizzazione della produzione a circuito chiuso, estendendo il flusso di lavoro integrato per supportare le esigenze specifiche dell'azienda. Sono previste personalizzazioni e integrazione con altre applicazioni, come i sistemi che gestiscono i processi di ricerca e sviluppo o della supply chain (spedizione e ricezione).
I nostri partner tecnologici
Riteniamo che l'innovazione separi i leader di settore da chi resta indietro. Anche le crescenti richieste di integrazioni end-to-end richiedono una stretta collaborazione tra le partnership tecnologiche. La nostra rete di partner globali ci permette di accedere ai software più all'avanguardia e alle ultime tecnologie sul mercato. Queste alleanze, come con SAP e Siemens, ci consentono di tessere flussi di dati complessi tra le soluzioni al fine di predisporre digital thread completi lungo l’intero ciclo di vita del prodotto. Di conseguenza, possiamo offrire soluzioni su misura per i nostri clienti, che contribuiscono a garantire il successo delle loro iniziative di trasformazione digitale.
Perché il Gruppo Engineering
Il numero di sistemi utilizzati per snellire e controllare il processo di produzione cresce esponenzialmente con il progredire della tecnologia. I produttori fanno affidamento su questi sistemi per far sì che i loro prodotti arrivino ai consumatori in modo efficiente e redditizio. Tali sistemi non sono solo utili, ma sono necessari sul mercato altamente competitivo di oggi. Per utilizzarli al massimo delle loro potenzialità, questi sistemi devono comunicare e funzionare in modo unificato. Per realizzare quest’integrazione, sono necessarie un'ampia esperienza top-bottom, una conoscenza approfondita dei processi industriali e un comprovato successo di implementazione. Il Gruppo Engineering è una delle poche aziende al mondo che può vantare sia la visione sia le competenze necessarie non solo per parlare di produzione intelligente, ma per renderla una realtà per le organizzazioni industriali di tutto il mondo.
Interessato a parlare con uno dei nostri esperti? Contattaci a [email protected].
creaz