Manufactura de bucle cerrado, hecha realidad
Integración de ERP, PLM y MES para lograr manufactura inteligente
Antecedentes
La digitalización está cambiando la forma en que las y los humanos vivimos y comportamos en muchas formas. Este fue un gran impacto en casi todos los aspectos de la sociedad. Tan solo considere la manufactura. Las fábricas han usado aplicaciones digitales por décadas, pero el impacto de un nuevo paradigma tecnológico cimentado en el Industrial Internet of Things (IIoT) y concretado en el concepto de Industry 4.0, está guiando el mundo de la manufactura hacia un campo de juego completamente diferente.
Entra en escena la manufactura inteligente, donde nuevas perspectivas habilitan las estrategias de producción para evolucionar en forma tal que promueve la optimización de procesos, el apoyo a decisiones inteligentes y la mejora continua de productos, procesos y personas.
Así pues, ¿cómo logramos esto? Es simple: con información y conectividad. Los datos son la llave, y la integración, en un sentido amplio, es la herramienta que habilita la manufactura inteligente.
¿Quiénes son los jugadores? Habrá que considerar a las compañías, los clientes y asociados, a los proveedores y concesionarios como los actores clave en la cadena de suministro moderna, a través de los cuales la generación, uso y compartición de datos funge como el cimiento para procesos eficientes y creación de valor.
¿Por qué la integración? La integración de aplicaciones digitales habilita la compartición efectiva de datos. Una forma eficiente de procesar y analizar datos puede generar un cuerpo de entendimiento informado con elementos que abonan a cada fase del ciclo de vida del producto. Al contar con la información apropiada, todas las funciones de la compañía se hacen más sostenibles, más eficientes, más proactivas y, lo más importante, más capaces de generar valor de negocio.
En sucesión a este enfoque de integración, se crea un proceso continuo único denominado manufactura de bucle cerrado, e incluye planeación de negocio, diseño de producto, planeación de manufactura, ejecución de producción y entrega de producto.
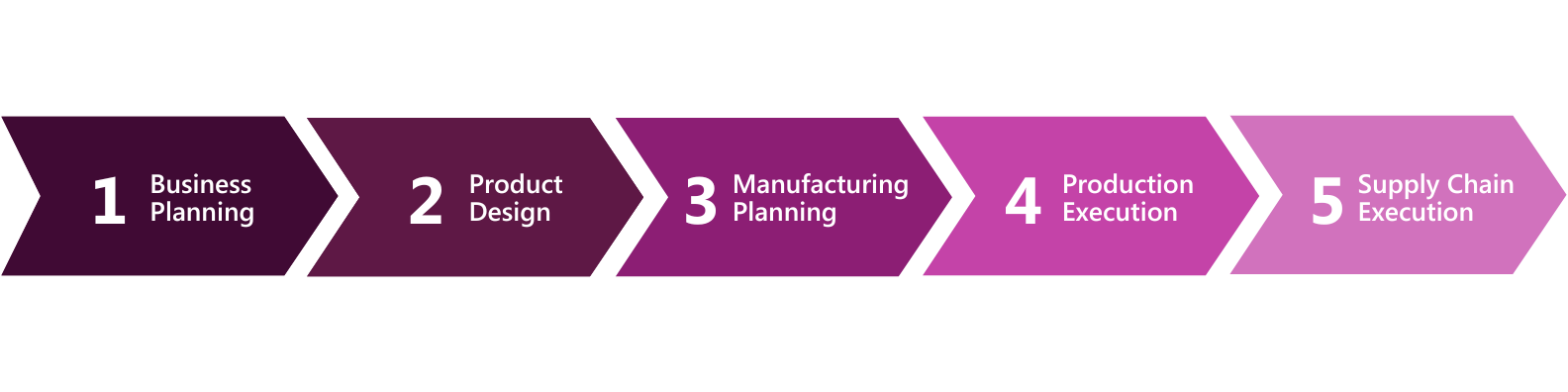
La propuesta
Teniendo presentes estos conceptos, Engineering Group ha combinado el poder de nuestro expertís en procesos de negocios, experiencia multiindustria y conocimiento técnico profundo de las aplicaciones industriales principales en el mercado para entregar una visión de la manufactura inteligente que pueda verdaderamente concretarse hoy día.
En términos de software, cuando Product Lifecycle Management (diseño de producto y planeación de manufactura), Manufacturing Execution Systems (ejecución de producción y control de calidad) y Enterprise Resource Planning (planeación de negocios, gestión inteligente de activos y entrega de productos) se integran, la suma, como en ocasiones ocurre, resulta ser más grande que cualquiera de sus partes individuales.
En términos de integración, los centros de competencia globales de Engineering Group proporcionan las capacidades críticas necesarias para zanjar la brecha entre negocios, ingeniería y operaciones. Nuestros equipos de Engineering Industries eXcellence y Engineering Enterprise Solutions han combinado la profundidad de experiencia y recursos capacitados necesarios para diseñar, implementar e integrar procesos y tecnologías a lo ancho de PLM, MES y ERP para así entregar una metodología integrada que habilita a las organizaciones de manufactura en la extensión de todos los sectores industriales a nivel mundial para llevar sus visiones de manufactura inteligente a buen término
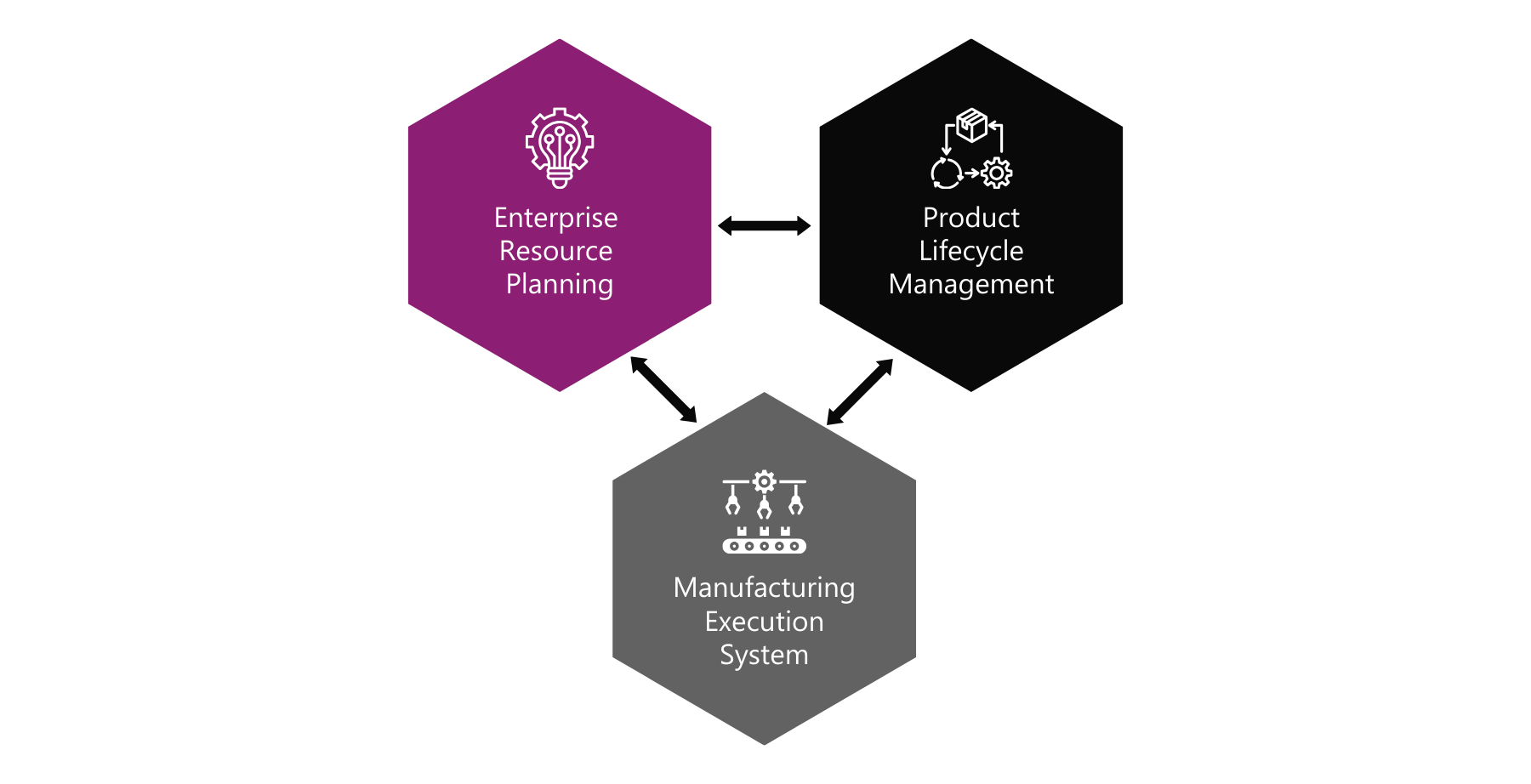
Los requisitos de negocio
La manufactura inteligente habilita la producción sustentable y eficiente de forma natural. El requerimiento clave es que, en cada una de las etapas del proceso de producción, toda la información relevante debe estar disponible, de forma que se pueda tomar la decisión correcta, o que el procedimiento correcto se active automáticamente. Los datos que componen esta información se puede generar en muchas partes y de muchas formas diferentes.
Los diseños de producto, equipo de producción, sistemas de prueba de producción y hasta los bienes producidos son todos fuentes de lo que llamamos datos de front-end. Estos datos se manejan mediante PLM, MES y aplicaciones operativas relacionadas.
Al mismo tiempo, los datos de back-end, cosa manejada mediante ERP y aplicaciones de negocio relacionadas, también son una fuente muy relevante e importante de información que impacta la producción. Como ejemplo de estos datos se incluyen las solicitudes de clientes, pedidos, disponibilidad de partes, cronogramas de mantenimiento, planes de turnos para recursos humanos, y demás.
Los datos de cadena de suministro de entidades externas tales como Asociados, Proveedores y Distribuidores también necesita ser parte del mosaico de datos ya que proporciona partes y servicios necesarios para la ejecución tanto de la producción como procesos de entrega. La gestión de información logística y de materiales que proviene de almacenes de producto y redes de transporte juega también un rol relevante.
Encima de todo ello, no olvide los datos de mercado relativos a demanda, economía/finanzas, disponibilidad de inventario, necesidades de reabastecimiento, guías regulatorias y mucho más.
Al considerar todo, el panorama de datos parece avasallante. Para permitir una gestión de operaciones efectiva, esta vasta colección de datos primero precisa recolectarse, luego analizarse y presentarse de forma oportuna, certera y atinada. Y para habilitar la verdadera manufactura inteligente, la inteligencia artificial y aprendizaje máquina deberán aplicarse a propulsar continuamente una toma de decisiones más optimizada, inteligente y ultimadamente, autónoma.
Los procesos soportados
Comprender y utilizar el poder de los datos es crítico para la manufactura inteligente, pero no resulta suficiente. ¿De qué manera las fuentes diferentes de datos que observamos interactúan e impactan una a la otra? Debemos entender esto con el fin de crear un plan de integración factible, que conectará exitosamente todos los procesos diferentes que entran en juego con la manufactura en toda la organización. Al cerrar el bucle y tener datos disponibles en la forma correcta, la producción es eficiente y la calidad aumenta.
Tomemos como ejemplo la industria de manufactura de alimentos y bebidas. ¿Cuáles son los procesos en juego? ¿Qué grupos de negocio y departamentos están involucrados? ¿Cómo interactúan estos con la producción? ¿Cómo les impacta la producción?
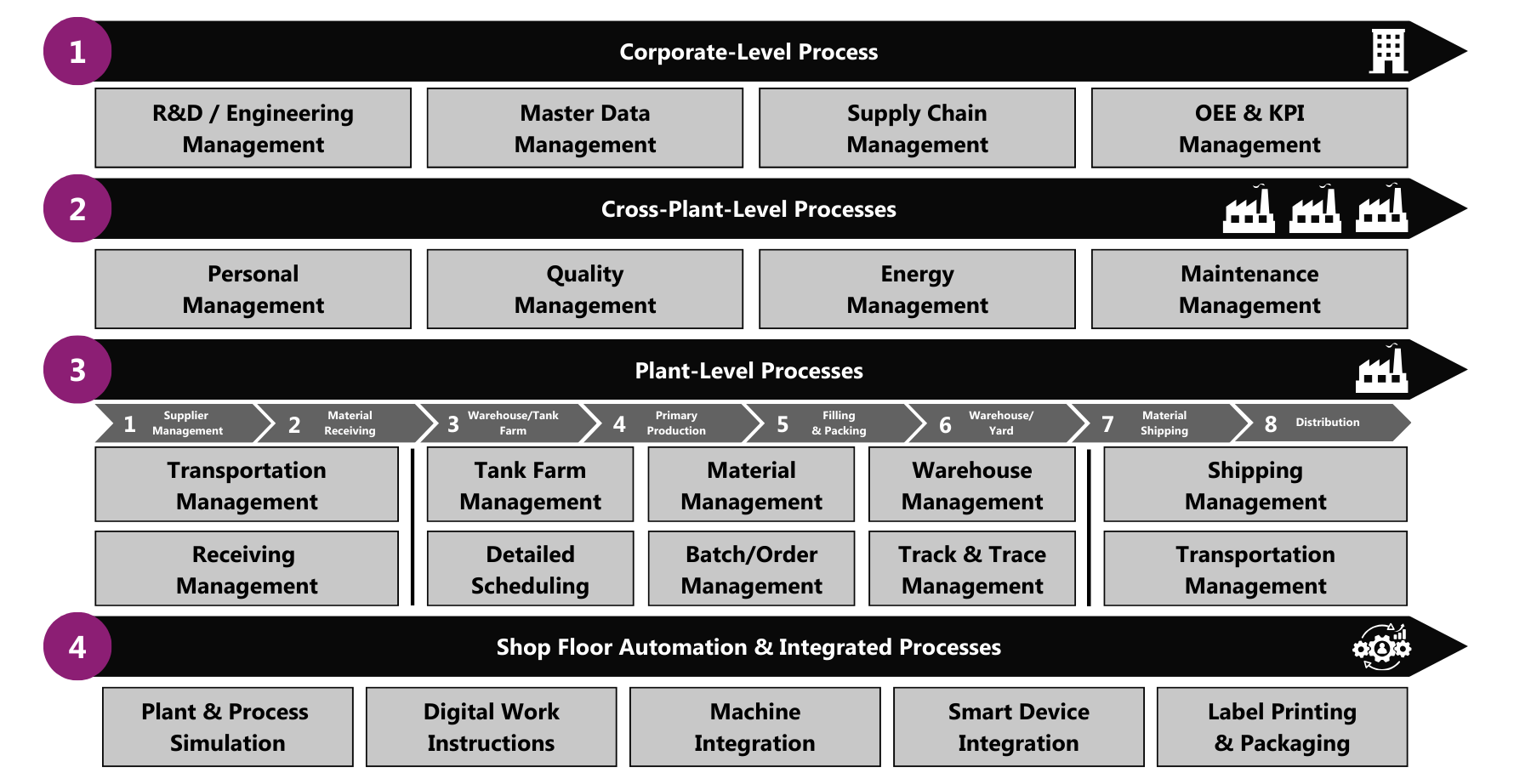
Nivel 1: Procesos a nivel corporativo
Al nivel corporativo, hemos establecido un conjunto de procesos que son comunes en toda la empresa organizacional. Estos se integran verticalmente y se comunican hasta que alcanzan al equipo en el piso de fábrica.
Por ejemplo, los cambios en diseño de producto por parte de ingeniería se alimentan descendientemente y a través de toda la empresa, señalizando los cambios en planeación, procuración, operaciones y ultimadamente cómo se fabrica el producto en la planta.
Nivel 2: Procesos a nivel multiplanta
Al nivel multiplanta, hemos establecido un conjunto de procesos que deberán gestionarse y evaluarse en conjunto, a través de las funciones de negocio y actividades, usualmente porque existe una necesidad fuerte para su estandarización en las plantas.
Por ejemplo, para comparar la eficiencia de sitios diferentes, las compañías deberán definir cómo medir indicadores de desempeño clave de forma estandarizadas, en términos de OEE, rendimiento, utilización de recursos, consumo energético, etc.
Nivel 3: Procesos a nivel de planta
Al nivel de planta, tenemos un conjunto de procesos cuya planeación de alto nivel se inicia al nivel corporativo, luego alimentados a través de operaciones y ejecutados finalmente a nivel detallado en la planta individual.
Por ejemplo, los pedidos generados por ventas para satisfacer una nueva demanda o solicitud de cliente se programarán para producirse en una región, planta o línea específica con base a restricciones, requerimientos y prioridades diferentes.
Nivel 4: Procesos integrados en piso de producción
La integración de activos y procesos en piso de producción al flujo de trabajo de manufactura inteligente habilita la optimización y mejora continua de actividades conforme las ejecutan personas y máquinas en el piso de fábrica.
Por ejemplo, la integración de dispositivos inteligentes para monitoreo del desempeño de activo habilita a los administradores de planta para supervisar la producción en tiempo real. Como resultado, pueden reaccionar más rápido a eventos imprevistos y en consecuencia prevenir interrupciones costosas.
La arquitectura técnica
Para habilitar la manufactura inteligente por medio de flujos de trabajo de datos de bucle cerrado, la clave es consolidar la integración de PLM, MES y ERP mediante interfaces técnicas bidireccionales. Los tres sistemas, una vez integrados, se hacen interdependientes, y la arquitectura técnica resultante es apta para sustentar al proceso completo de ciclo de vida de producto de inicio a fin:
- Product Lifecycle Management (PLM) proporciona capacidades de gestión de datos para el diseño de productos, definición de productos, planeación de calidad, planeación de procesos de manufactura, configuración de productos y gestión de cambios;
- Manufacturing Execution Systems (MES) brindan capacidades de ejecución operativa para ejecución de órdenes de producción, recolección de datos de producción, recolección de datos de calidad, pruebas de calidad y confirmación de producción;
- Enterprise Resource Planning (ERP) proporciona capacidades de negocio de alto nivel para planeación de ventas, operaciones de cadena de suministro, planeación de manufactura, procuración, gestión inteligente de activos y gestión de recursos en toda la empresa.
La meta de integración es implementar la Digital Thread, un flujo continuo de datos que asegura que toda la información correcta esté disponible cuando y donde se necesita. La arquitectura técnica resultante entonces se vuelve el cimiento de su organización para sus plantillas de procesos de negocios para manufactura de bucle cerrado.
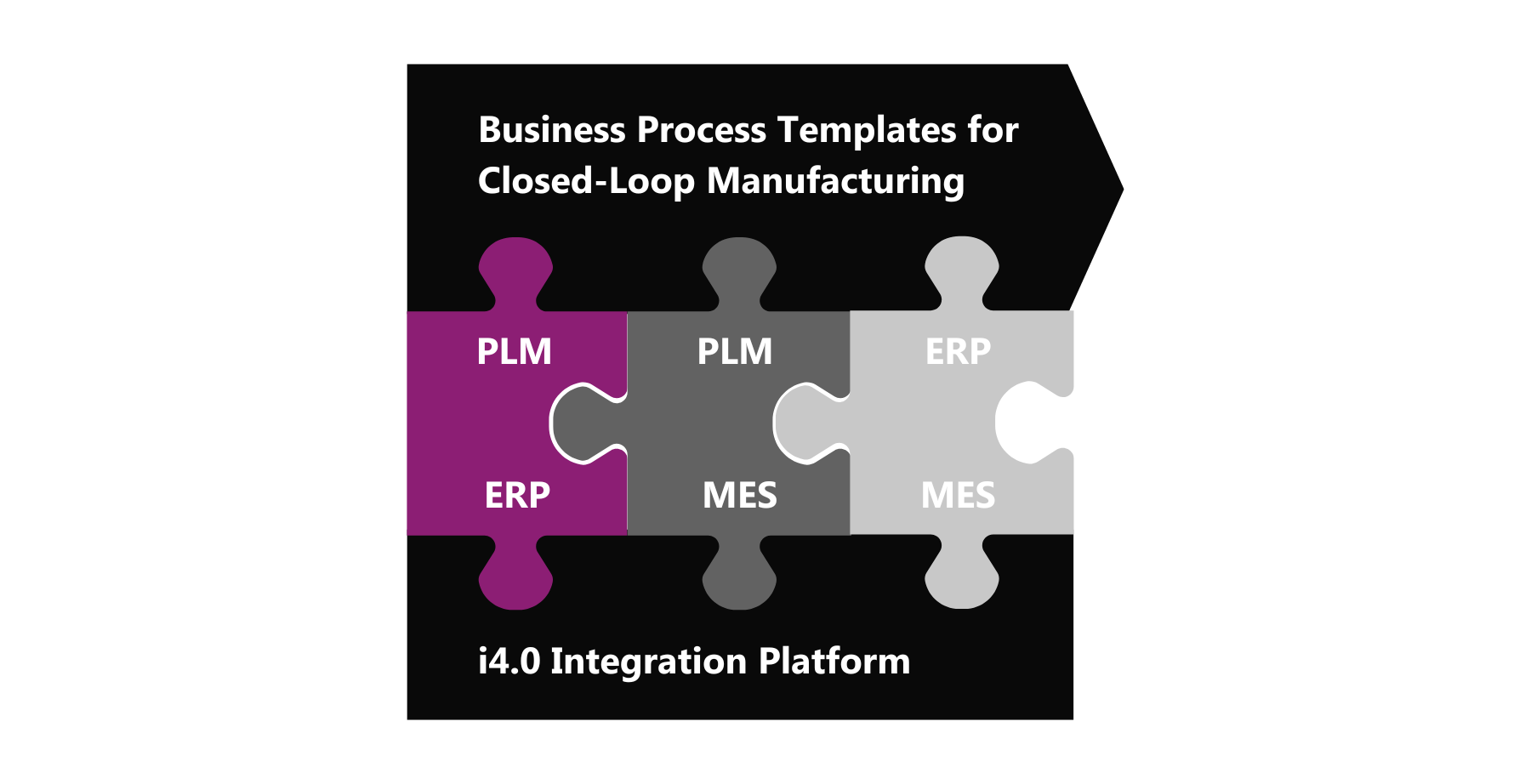
Interfaz: Integración ERP a PLM
La primera interfaz bidireccional implementada proporciona el vínculo colaborativo entre PLM y ERP, así asegurando que el sistema de registros para productos en PLM alimente el sistema de registro para planeación de negocios en ERP. El sistema PLM gestiona los datos de productos desde el diseño inicial, conforme este se revisa y mediante la liberación para producción, en tanto que el sistema ERP utiliza la verdad del producto que proporciona PLM para planear con exactitud y gestionar recursos de productos y finanzas. Esta sincronización mediante integración es clave para conducir el desarrollo innovador de productos y el lanzamiento rentable de productos.
Interfaz: Integración PLM a MES
La segunda interfaz bidireccional implementada proporciona el vínculo colaborativo entre PLM y MES, extendiendo así el valor de las amplias capacidades de gestión de datos de un PLM desde diseño y planeación de manufactura hasta la ejecución del flujo de trabajo de producción. Esta integración crea una única fuente de verdad durante todo el ciclo de vida del producto, asegurando que cada pedido ejecutado en la fábrica se logre en línea con todas las especificaciones de productos y procesos. Como resultado, la calidad se controla y verifica, el riesgo de costosos reprocesos se elimina y se reduce significativamente el tiempo a mercado.
Interfaz: Integración ERP a MES
La tercera interfaz bidireccional implementada proporciona el vínculo colaborativo entre ERP y MES, asegurando la completa alineación entre las funciones de planeación de negocio y producción de la organización. Esta integración habilita el intercambio oportuno de información crítica entre redes de ventas, procuración y proveedores con actividades en tiempo real en el piso de fábrica. Los datos compartidos y sincronizados mediante integración pueden incluir el estatus y disponibilidad de materias primas, bodegas, inventario de productos, gente, activos, equipos y datos.
Conexión: Plataforma de integración i4.0
Todas las tres interfaces técnicas bidireccionales se conectan a la plataforma de integración i4.0, un concentrador centralizado basado en nube que proporciona todos los servicios requeridos para materializar y gestionar las interconexiones e interfaces multisistema. Se diseña y construye la plataforma flexible de forma que da a las organizaciones de manufactura las opciones para extender estas capacidades a y desde otros sistemas o aplicaciones corporativas si y cuando se desee.
Diseño de la solución
La transformación digital significa usar tecnología para crear (o modificar los existentes) procesos de negocio y adaptarse a las demandas del mercado. Una estrategia de digitalización efectiva comienza con una evaluación a profundidad de los procesos de la compañía "como están", cuyos resultados en turno dirigen el diseño de una solución holística "como será" capaz de satisfacer todas las necesidades funcionales y de negocio.
Qué: Mapas de procesos y plantillas
Para ayudar a las compañías industriales a controlar e integrar todos los flujos de información que entran en juego con la manufactura, hemos establecido un conjunto probado de plantillas específicas por industria y metodologías de mejores prácticas. Estas se utilizan para documentar procesos, tanto manuales como automatizados, a través de diferentes departamentos de la empresa, con el fin de crear un mapa visual de cómo interactúan uno con el otro y con las operaciones de fábrica. Al usar este mapa de ruta, podemos asegurarnos de que no se ignore proceso alguno en el diseño de la solución final.
Quién: Diseño de aplicación basado en roles
El rol de las personas también habrá de considerarse y desarrollarse en la estrategia de digitalización desde el principio. ¿Cómo podemos asegurar que entregamos valor enfocado en usuarios? ¿Cómo podemos asegurar que la infraestructura digital se construye en forma tal que sustenta a la gente y su mejora continua? Hacemos esto al recolectar los requerimientos de usuarios en un principio y al colaborar con ellos y otros interesados durante todo el proceso de desarrollo.
Cómo: Metodología de digitalización bimodal
Nuestras plantillas de procesos de negocio específicas por industria se construyeron con el objetivo de aparear una evolución más predecible de productos y tecnologías estándar con las metodologías más novedosas e innovadoras para la digitalización. Esta es la esencia de lo que Garner ha llamado la Metodología de digitalización bimodal de dos velocidades.
Cuando se implementa correctamente, esta metodología para el diseño de soluciones promete el camino más rápido y efectivo hacia la manufactura inteligente para organizaciones industriales en todos los sectores. La metodología de dos velocidades afirma que el mapa de ruta de una organización para Industry 4.0 deberá considerar e incluir dos arquitecturas de solución separadas (empero, simultáneamente ocurrentes y complementarias):
- Modo 1 concentrado en PREDECIBILIDAD y CONFIABILIDAD (p. ej.: sistemas centrales como ERP, PLM, MES, QMS, etc.);
- Modo 2 concentrado en AGILIDAD y EXPLORACIÓN (p. ej.: tecnologías habilitantes: Cloud, Low Code, AI, etc.).
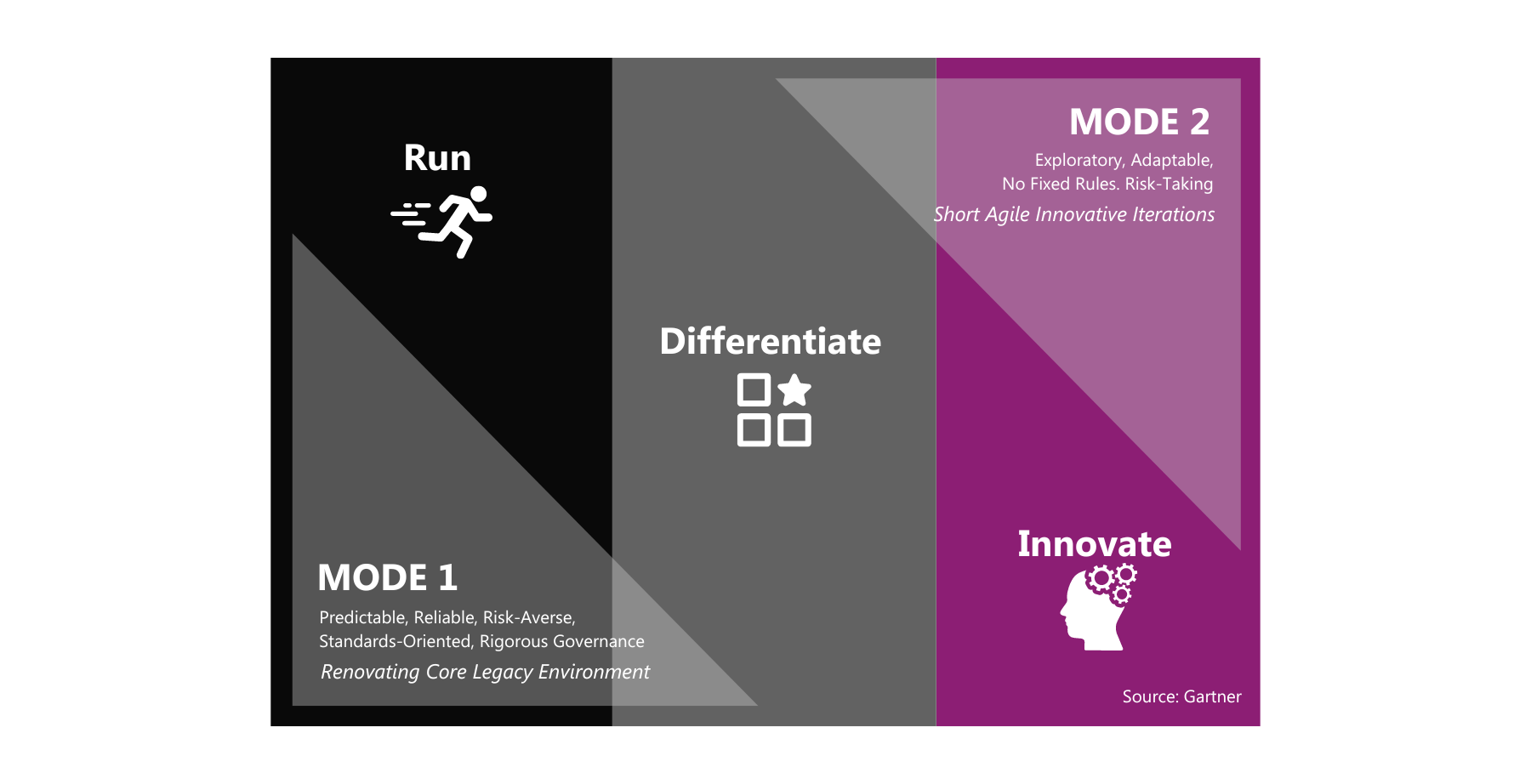
Construcción de la solución
Cada segmento del plano de solución diseñado se desarrolla y valida siguiendo la metodología propietaria de implementación de software de nuestra organización: ENGILE.
ENGILE combina una metodología ágil innovadora con ítems específicas de la metodología tradicional de cascada para el desarrollo de software. Como resultado, no solo podemos entregar soluciones integradas de manufactura de bucle cerrado de forma más rápida y efectiva en costo que cualquier otro integrador de sistemas en el mundo, sino que además lo hacemos al nivel de calidad más alto.
Está comprobado que la metodología ENGILE minimiza riesgos, aumenta el control y logra los objetivos de proyecto a tiempo y tal cual se espera.
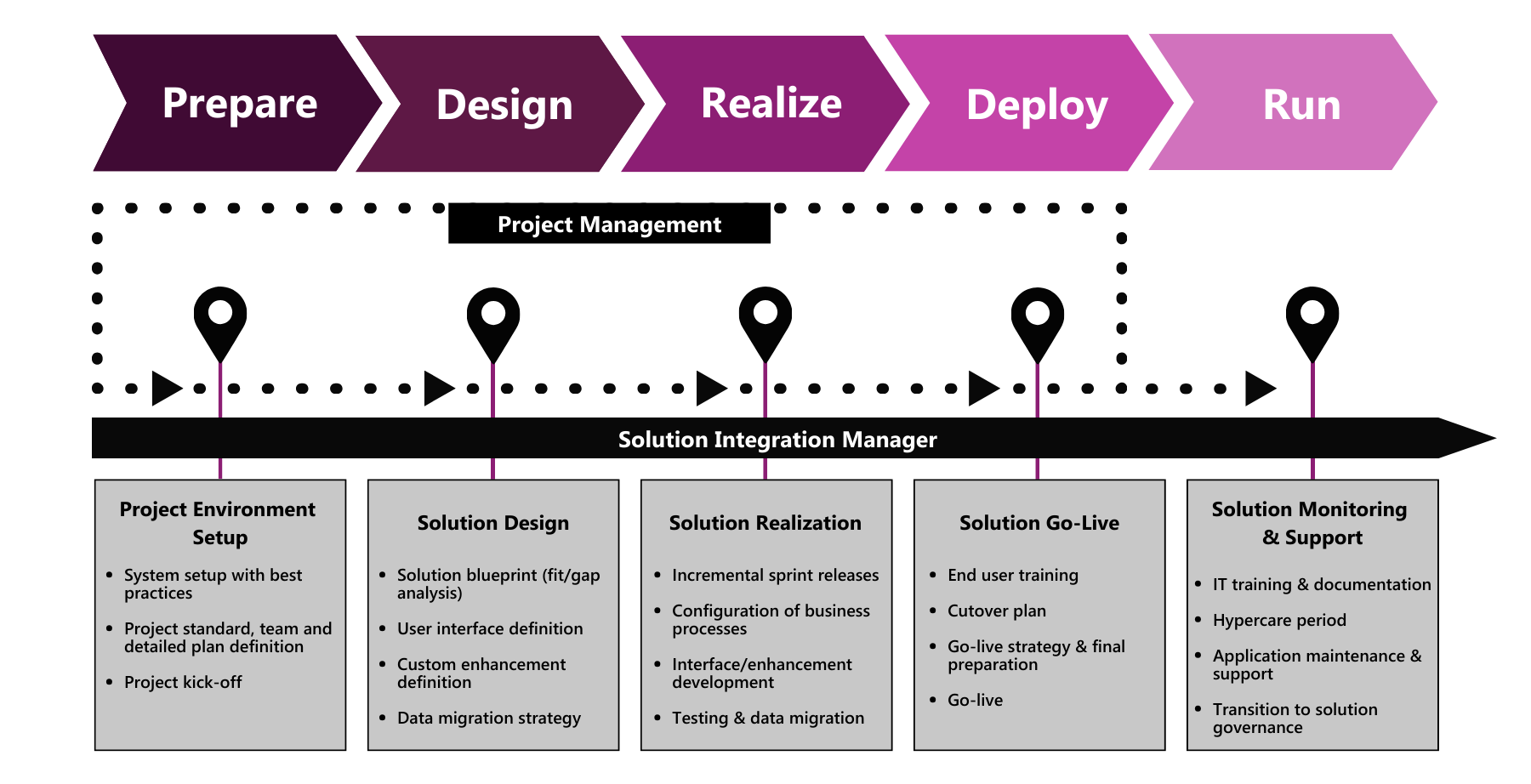
Entrega del proyecto
Una metodología típica de la entrega exitosa de un proyecto de manufactura de bucle cerrado comienza con un piloto o prueba de concepto, seguido por tres fases de implementación:
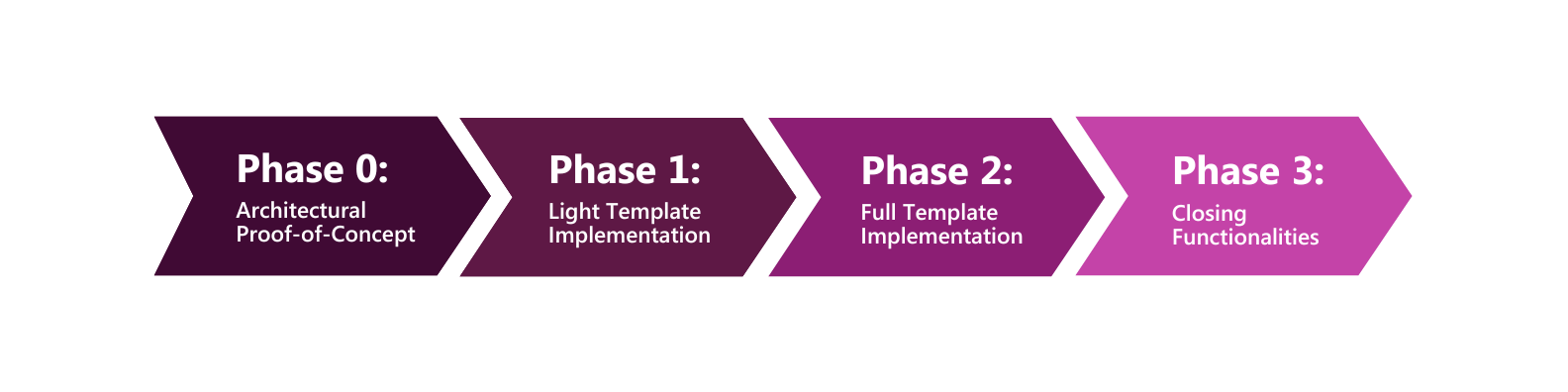
Fase 0: Prueba de concepto
La prueba de concepto apunta a probar funciones y capacidades destacadas de la solución final en una planta o línea de producción seleccionada con el fin de asegurar la viabilidad de la solución sin arriesgarse a interferir con las operaciones de planta o negocio. Este también es el punto de inicio para el diseño del ambiente de plataforma de integración i4.0 en la nube, considerando conectividad con las interfaces técnicas bidireccionales a establecerse en la fase siguiente.
Fase 1: Implementación de plantilla ligera
La implementación de plantilla ligera busca extender la prueba de concepto para cubrir un mayor número de plantas y/o líneas de producción. También incluye la implementación de la primera versión de la arquitectura de integración, estableciendo la conexión entre interfaces bidireccionales y la plataforma de integración i4.0 y validando funcionalidades críticas de recolección y gestión de datos.
Fase 2: Implementación de plantilla completa
La implementación de plantilla completa libera todas las funcionalidades remanentes de la solución integrada ERP a PLM a MES como se diseñó. Esta fase incluye actividades que personalizan las capacidades de la plataforma de integración i4.0 a la nube. Los servidores locales, todos integrados con la plataforma, también se pueden instalar para mejorar un mayor control en sitio.
Fase 3: Funcionalidades de cierre
La fase de funcionalidades de cierre busca completar la realización de manufactura de bucle cerrado al extender el flujo de trabajo integrado para soportar necesidades específicas por organización. Esto incluye customizaciones e integración a otras aplicaciones, tales como sistemas que gestionan procesos de investigación y desarrollo o cadena de suministro (envío y recepción).
Nuestros asociados tecnológicos
Creemos que la innovación separa los líderes de la industria de los retrasados. Las demandas en continuo incremento para las integraciones de inicio a fin también requieren colaboración estrecha entre asociaciones tecnológicas. Nuestra red global de asociados nos da acceso a la tecnología más avanzada en el mercado. Estas alianzas, tales como SAP y Siemens, nos permiten crear flujos de datos complejos entre soluciones, para fabricar digital threads completas de ciclo de vida de producto. Como resultado, podemos ofrecer soluciones a la medida para nuestros clientes, que ayudan a asegurar el éxito de sus iniciativas de transformación digital.
Por qué Engineering Group
El número de sistemas que se utilizan para depurar y controlar el proceso de manufactura crece exponencialmente conforme la tecnología progresa. Los fabricantes confían en estos sistemas para traer sus productos a clientes de forma eficiente y rentable. Estos sistemas no son meramente algo que es bueno tener; se les requiere en el mercado altamente competitivo de hoy. Para utilizarles hasta su completo potencial, estos sistemas necesitan comunicarse y operar de forma unificada. Para lograr esta integración, se requiere tanto expertís amplio desde la parte alta de la pila hasta el fondo, conocimiento profundo de procesos industriales, así como el éxito probado de implementación. Engineering Group es una de las pocas compañías en el mundo que cuenta tanto con la visión como con las habilidades necesarias para no solo hablar acerca de manufactura inteligente, sino de hacerla una realidad para organizaciones industriales en todo el mundo.