Product Lifecycle Management
What is Product Lifecycle Management (PLM)?
Product Lifecycle Management, or PLM, is the process of managing the complete lifecycle of a product from ideation, through engineering design and manufacturing, to service and disposal. PLM systems are built to integrate product data with business processes and systems. They provide a centralized location for each detail of design and manufacturing including Bill of Materials (BOM), compliance records, manufacturing tools and resources libraries, digital work instructions, etc. Companies can leverage PLM systems to collaborate instantly throughout the product design and process planning of piece-part manufacturing and assembly processes and operations.
Why Use PLM Systems?
Organizing and managing large amounts of data is a huge task in the manufacturing industry. Furthermore, keeping this information up-to-date as well as making sure that data is controlled and accessible between different departments across an enterprise organization is a big challenge. Within a PLM system, teams and individuals can create, organize, manage and consolidate information effectively.
From Design to Manufacturing: Closing the Loop
PLM systems promote accurate and informed decision-making throughout the lifecycle of the product. They offer several features designed to significantly increase productivity across multiple disciplines. Starting with product design, PLM systems store 3D data as well as detailed properties of assemblies and components. The product design is revision controlled, allowing continuous updates and improvements, while also restricting user access and tracing the maturity status. Manufacturing can then use the design information to create a detailed manufacturing routing which can be passed to downstream systems such as Enterprise Resource Planning (ERP) and Manufacturing Execution Systems (MES). In addition, PLM systems can be integrated with simulation tools, as a result allowing companies to optimize the manufacturing process from details of robotics and ergonomics to plant simulation.
Features of PLM Systems
- Design and process document management
- BOM configuration management permitting variability to support the entire scope of a product’s configuration
- Embedded viewer enabling the user to visualize and manipulate 3D product designs
- Defined company organizational structure allowing designated access control
- Automated digital workflows designed to capture business procedures in which documents, information or tasks are passed from one user to another
- Extensive reporting capabilities
- Integrated with simulation tools
- Integrated with other business processes such as Enterprise Resource Planning (ERP) and Manufacturing Execution Systems (MES)
Benefits of PLM Systems
- Flexible, automated business processes
- Version control enabling BOM evolution and continuous process improvement
- Effective collaboration and communication across disciplines
- Improved productivity and minimized rework with visibility of up-to-date and accurate BOM information
- Optimized changed management process with a clear understanding of impacted data, users and processes
- Greater traceability for product changes and updates
- Reduced costs due to extensive re-use of documentation
- Maximized lifetime value of the product
To learn more about our digital tool offering for PLM, click here.
Interested in speaking to one of our experts? Contact us at [email protected].
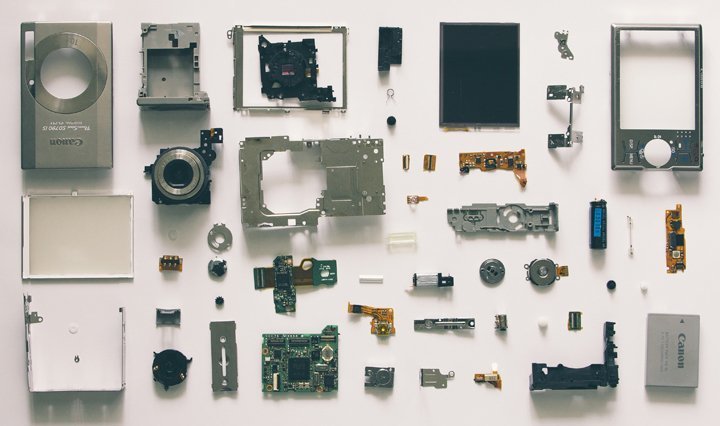