Robotic & Human Ergonomics Simulation
How Robotic & Human Ergonomics Simulation Works
As new product designs are introduced by engineering, it is important to evaluate those designs and then pass that information on to downstream systems and organizations. This is the start of the Digital Thread for a product. In this process, it is important not just to run engineering simulations on the product, but also manufacturing simulations.
Can we feasibly build the product based on our design? Will it meet cycle time requirements that we are expecting? All of these questions can be answered by running simulations of the process within a simulation tool. The process simulation can take many factors into consideration, looking at both the human and machine manufacturing processes. Modeling humans, robots, conveyors, tools and other typical process elements is becoming critical during new product launches or introductions to truly understand the process and find ways to optimize it for business profitability.
What is Robotic & Human Ergonomics Simulation?
Robotic & Human Ergonomics Simulation is a technology-driven methodology that offers insights into real-world processes through the modeling of those processes in the digital world. Simulation modeling when it comes to robotic or human activities involves evaluating current circumstances, replicating the behavior of events and implementing algorithms that analyze and test scenarios for operational optimization. It is a technique used across a variety of industries to lower costs and improve decision-making.
The increased complexity of products and manufacturing processes presents world-class manufacturers with increasing challenges to minimize “time-to-market” and optimize asset performance. Manufacturing engineering teams are expected to enable flawless new product launches and adhere to cost, quality and start-of-production targets. To overcome these challenges, leading manufacturers leverage their organizational knowledge and the availability of 3D models of products and resources to virtually validate their manufacturing processes before they are deployed in the real world. With new evolving technology, thousands of validation experiments can be conducted efficiently and almost automatically to ensure upfront production optimization.
Features of Robotic & Human Ergonomics Simulation Solutions
- Robotic process simulation modeling
- Human task simulation modeling
- Resource measurement, design and modeling (2D, 3D, kinematics)
- Bottleneck and issue detection analysis
- Assembly and robotic path planning
- Production line and workstation design
- Static and dynamic collision detection
- Human reach envelopes, vision window and postures
- Event-driven simulation studies
- Ergonomics and safety studies
- Discrete and process event simulation
- Sequencing of operations
- Assembly time studies
- Robotics studies on placement, reach, cycle times and offline programming
- Validation of mechanical/electrical production processes (PLCs/robotics)
- Validation of new production commissioning
- KPI definition, monitoring and analytics reporting
Benefits of Robotic & Human Ergonomics Simulation Solutions
- Detect and eliminate issues ahead of production
- Minimize risks and costs in production
- Maximize use of manufacturing resources
- Optimize production cycle times and processes
- Ensure ergonomically-safe processes for employees
- Increase efficiencies and process quality
- Reduce time-to-market
- Drive smarter decision-making
- Justify optimal investment initiatives
- Maximize profitability for new product introductions
Engineering’s Expertise
Our team specializes in applying simulation methods to operational systems, processes, facilities and enterprises. Our consultants help organizations identify opportunities in order to strategically employ simulation to study manufacturing processes and systems, giving teams the information and tools they need to drive real improvements.
Interested in speaking to one of our experts? Contact us at [email protected].
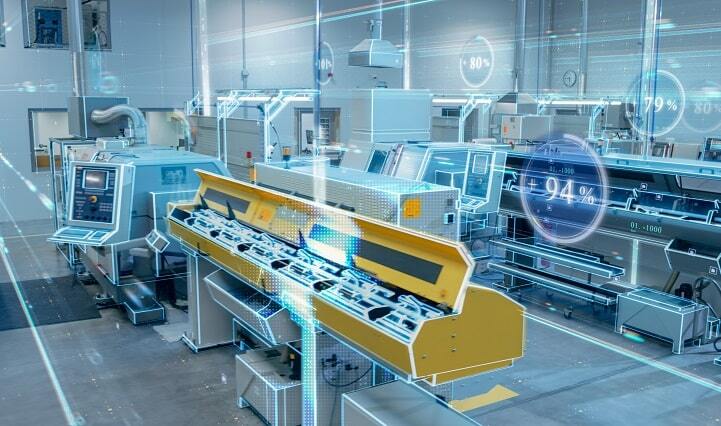