Field Service Management
Today’s Manufacturing Landscape
In today’s manufacturing landscape, characterized by increasing restrictions and asset complexity, organizations worldwide are facing major challenges when it comes to carrying out their traditional approach to workforce management and task planning, in particular when critical asset maintenance is concerned. In order to run their operations smoothly, manufacturers are required to periodically inspect and maintain a multitude of critical equipment and machineries, which are, no matter how high-quality, still subject to failure and breakdown. For this reason, industrial enterprises must have the right solutions and processes in place to help them deal with the continuous number of on-site plant inspections, maintenance activities and urgent work orders that need to be planned and dispatched to frontline workers on a daily, weekly and even long-term basis.
What is Field Service Management (FSM)?
In light of these demands, manufacturers today are turning to digital solutions in order to automate, streamline and effectively execute the multitude of Field Service Management (FSM) activities on their plate. Digital solutions for Field Service Management (FSM) are designed to help organizations increase the efficiency of their operations, improve shop floor maintenance processes and prevent costly downtimes. Effective software solutions for Field Service Management enable enterprises to manually and automatically plan and assign tasks, manage workforce agendas and support technicians in the performance of complex, risk-sensitive activities.
Industrial Field Service Management (FSM) solutions are specifically designed to facilitate the planning, optimization and dispatch of different activities and orders to frontline teams working on technical assets in the field, on a customer’s premises or in a production plant. The activities covered by Field Service Management (FSM) technologies typically include support, installation, repair, inspection and maintenance tasks, which are often defined in a service or maintenance contract and require specific equipment and materials. Authorized internal staff as well as contractors are able to use the system to view and collect information regarding their activities through a mobile device (e.g. smartphone, tablet, wearable device).
Appointment-centric and asset-intensive industrial enterprises can greatly benefit from the adoption of digital Field Service Management (FSM) solutions in order to increase efficiency and service quality levels, while reducing or avoiding costs at the same time. In fact, according to leading research and consulting companies in the IT sector, the Field Service Management (FSM) market registered a business volume of over $ 2.5 billion in 2019, and exceeded its growth by 26% compared to the previous year.
Features of Field Service Management (FSM) Solutions
- Manage Field Service demand, activities, assets and resources
- Generate Field Service requests, tasks and/or orders
- Acquire intervention requests (from internal and external systems)
- Manage preventive and corrective maintenance tasks
- Predict Field Service needs, even with Artificial Intelligence (AI)
- Plan on a short-term, medium-term and/or long-term basis
- Plan at a team-specific, site-specific, asset-specific and/or enterprise level
- Schedule and optimize Field Service activities
- Assign and dispatch Field Service tasks to frontline workers and/or teams
- Manage and enforce Field Service data collection
- Enable Field Service technicians and debrief tasks in mobility
- Enable Field Service workers to operate hands-free
- Provide remote task guidance and digital work instructions to workers executing in the field
- Enable on-the-spot access to digital documentation and multimedia resources, including 3D visualization and manipulation of asset Digital Twins
- Monitor Field Service workers, activities and task execution in real time
- Provide Internet of Things (IoT) data visualization from assets
- Manage additional operations, e.g. contractors, upselling services, warranties, projects, etc.
- Enable virtual workforce collaboration, even with Augmented Reality (AR)
- Manage Factory Acceptance Tests (FAT)
- Manage and improve enterprise knowledge, even with Artificial Intelligence (AI)
- Field Service performance reporting and analytics
Benefits of Field Service Management (FSM) Solutions
- Smarter planning of service tasks and resources
- Optimize allocation of resources
- Increase monitoring and control over shop floor operations
- Increase First Time Fix Rate (FTFR)
- Reduce asset downtimes and Mean Time Between Failures (MTBF)
- Minimize operational and training costs
- Improve workforce productivity and efficiency
- Improve Service Level Agreement (SLA) compliance
- Better support workers in the execution of inspection and maintenance activities
- Enable hands-free operativity
- Increase workforce safety and collaboration
- Streamline issue resolution and reduce Mean Time To Resolution (MTTR)
- Enhance enterprise training and knowledge management
- Facilitate workforce and service performance analysis
- Improve customer satisfaction
Engineering’s Expertise
Engineering Group has been an expert consulting partner, solution provider and system integrator in the industrial space for more than 3 decades, with established technology practices and specialized teams focused on the digitalization and advancement of the Manufacturing, Assembly, Transportation, Oil & Gas, and Energy & Utilities sectors. For many years, and together with OverIT Field Solutions, a company of the Engineering Group, we have been designing, developing and implementing industry-recognized Field Service Management applications for leading enterprises across all industrial sectors worldwide. Drawing on our long-standing expertise in mobile software development, Geographic Information Systems (GIS), Artificial Intelligence (AI) and Augmented Reality (AR) technologies, we build and deliver smart Field Service Management solutions to help organizations successfully coordinate, manage, control and optimize their Field Service and maintenance teams, activities and assets at the enterprise level.
Interested in speaking to one of our experts? Contact us at [email protected].
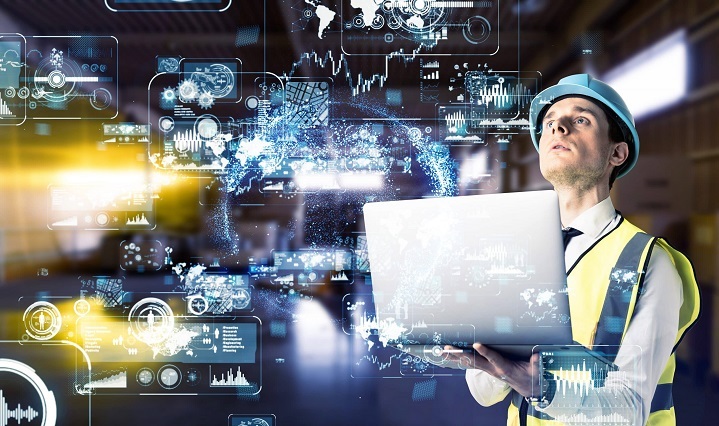