Direct Numerical Control (DNC)
Challenges of the Machining Shop
Whenever our team visits a machining shop floor, we can usually count on seeing at least one of the following:
- Numerical Control (NC) programs residing on individual machine controllers instead of in a centralized location;
- Computer-Aided Manufacturing (CAM) engineers putting their programs on a USB stick and manually whttps://www.indx.com/index.php...alking them to each machine where they will be run;
- Operators' knowledge about which program to run is based on "tribal knowledge" and word-of-mouth instead of reliable documentation;
- There is little or no revision control of NC programs;
- All documentation, including setup sheets at machining workstations, is paper-based;
- Machines experience frequent equipment downtimes without a process in place to understand why.
There are too many costly risks associated with these types of inefficient processes: running an outdated program, placing a program on the wrong machine or failing an audit, just name a few. Since Computer Numerical Control (CNC) machining manufacturers typically work with very expensive equipment and materials, these risks are both unacceptable for operations and unsustainable for the business. A company’s CAM engineers often know that this situation isn’t right, but they aren’t sure how to best address the issues. There is a solution. The answer to these problems, common in most machining shops, is a fully integrated and automated CNC machining environment involving the implementation of software tools for Direct Numerical Control (DNC) and Machine Data Acquisition (MDA).
What is Direct Numerical Control (DNC)?
The purpose of a Direct Numerical Control (DNC) system is to provide a central digital repository for all manufacturing and NC data, and to make this data available to the shop floor. Features of a complete DNC solution include:
- Central management and revision control of NC programs and related CAM data;
- Direct connection from the data repository to CNC machines on the shop floor;
- Configuration options to support specific requirements and preferences of each manufacturer.
What is Machine Data Acquisition (MDA)?
The purpose of Machine Data Acquisition is to collect information from shop floor equipment and make that information available to plant operators in order to assist manufacturers in identifying and addressing the biggest and most costly causes of their equipment problems and downtimes. Features of a complete MDA solution include:
- Central portal for accessing real-time and archived machine data;
- Real-time extraction of signals directly from shop floor equipment;
- Configurable reports to help manufacturers understand and improve their production performance and capabilities.
Features of Direct Numerical Control (DNC) Solutions
- Enable central management and revision control of machine programs and data (e.g. NC programs and CAM data)
- Provide a direct connection from centralized data repository to your machines and robots
- Download and upload production job data and tool target data to/from machine controllers
- Upload and manage machine programs programmed on the shop floor to data repository
- Upload and administer machine parameters in data repository to ensure security
- Connect to all types of machine controllers and tool presetters
- Connect to data repository through a serial (with adapter hardware) or Ethernet interface at the machine controller
- View all machining and manufacturing information via a browser-based interface on the shop floor
- Leverage system configuration options to support different machining requirements and user preferences
Benefits of Direct Numerical Control (DNC) Solutions
- Drive paperless manufacturing
- Ensure use of correct and current data in production
- Minimize production errors
- Standardize and control processes for change management
- Eliminate local shop floor databases outside of IT infrastructure
- Provide data transparency to all users
- Enable quicker and more flexible information flows
- Improve process efficiency and quality
- Lower product rejection rate
- Facilitate communication between engineering and manufacturing
Engineering's Expertise
Engineering is an expert system integrator of complete, end-to-end DNC systems. Our areas of expertise include CAM workflows and requirements, PLM integration and CNC machine connectivity. We have connected dozens of different CNC machine makes and models to state-of-the-start DNC systems for manufacturers across a number of different sectors.
Interested in speaking to one of our experts? Contact us at [email protected].
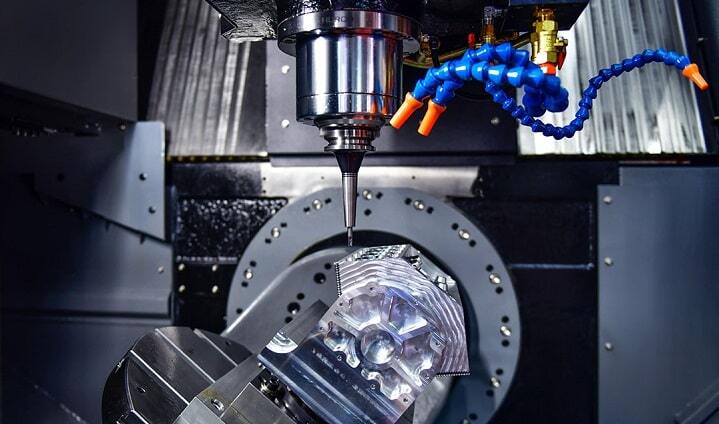