Siemens SINUMERIK Manage MyResources / Tools
About Siemens SINUMERIK Manage MyResources / Tools
Siemens Digital Industries is a global leader in CNC Shopfloor Management Software. SINUMERIK Manage MyResources / Tools , previously known as Shop Floor Integrate, is a software application within Siemens' leading SINUMERIK Integrate for Production suite designed for shop floor management, optimization and digitalization. Manage MyResources / Tools is a tool management software that enables machining and manufacturing enterprises to track and control the complete lifecycle of physical resources on the shop floor. Manage MyResources / Tools acts as the bridge connecting virtual tooling instances used by the manufacturing planning department with the physical tooling instances on the production floor.
Manage MyResources / Tools for Physical Tool Management
Manage MyResources / Tools creates physical tooling instances by pulling virtual tool data, such as required components and measurements, from the central Manufacturing Resource Library (MRL) within Siemens Teamcenter Manufacturing, and then makes this data easily available to operators on the shop floor. Once the tool assembly is built, Manage MyResources / Tools can integrate with a presetter to retrieve the actual tool measurements and store this data alongside the tool record in the central database. Manage MyResources / Tools also manages the tooling inventory in a shop, the planning of the number of additional tools that would need to be created to complete a job, as well as the loading and unloading of tools to machines. The system automatically synchronizes with Teamcenter, thus bridging the virtual and physical worlds of manufacturing, maximizing tool life and ensuring efficiency and quality across all your shop floor processes.
So, how does it work?
- A Computer-Aided Manufacturing (CAM) engineer designs the virtual tool in Siemens NX, then defines the virtual tool within Siemens Teamcenter’s Manufacturing Resource Library (MRL) application.
- The CAM engineer then pulls the tool data from Teamcenter MRL and uses it to generate the NC (Numerical Control) machining program within NX. The virtual tool in Teamcenter MRL is linked to all the machining operations for which that particular tool assembly is/was/will be utilized.
- When a tool request is sent to the shop floor tool manager, the tool manager uses the virtual tool definition stored in Teamcenter MRL to create a physical tool assembly on the shop floor. The tool manager then presets the physical tool assembly with a tool presetter.
- The physical tool, along with the measured data, is “stored” in the Manage MyResources / Tools application, and is ready to be used in production. The physical tool with the actual measurements is then sent to the relevant CNC (Computer Numerical Control) machine and loaded for production execution.
By digitalizing and connecting the entire Tool & Resource Management process, manufacturers enable their users to understand what tools are available and to efficiently determine which operations are affected when a physical tool is out of stock or when a component used in a tool assembly is discontinued. Engineers can run a quick analysis within Teamcenter to determine which machining operations would be affected when the tool is out of stock or being replaced by a new tool. As a result, they are able to preemptively update related NC programs as needed, preventing costly interruptions in production. By increasing visibility into existing inventory within the production facility and ensuring that they are only purchasing tools that are not currently on hand, Manage MyResources / Tools also enables manufacturers to reduce their tool inventory and the high costs associated with it.
Target Manufacturing Sectors
- CNC machining
- Piece-part manufacturing
- Assembly manufacturing
- CNC turning
- CNC milling
- CNC multi-tasking machining
- CNC lather
- CNC grinding
- CNC nibbling
- CNC laser cutting
- CNC plasma cutting
- CNC water jet machining
- Composite machining
- Additive manufacturing (material extrusion and laser cladding)
- Gear machining
- 3D printing
- Automated cell machining
- Robotics machining
- Pick and place machining
Features of Siemens SINUMERIK Manage MyResources / Tools
- Link virtual tool instances in Siemens Teamcenter Manufacturing database to physical tool instances in the plant
- Track and manage locations of physical tool instances on the shop floor
- Manage tool life and utilization history
- Search for tool, view status of tool (e.g. reservations) and access nominal tool data
- Provide tool assembly sheets displaying all components required to build a tool assembly
- View and add additional tooling inventory
- Configure and receive low tool stock notifications
- Create or import tool plan from Siemens Teamcenter Manufacturing database to understand what tools are required for a specific job and the usage time for each tool
- Create or link machining sequence(s) to tool plan indicating the machine(s) and quantity of production runs required
- Execute tool balancing to determine the number of tools required for selected machining sequence(s)
- Interface to tool presetter
- Manage tool preset data and transfer to NC machines
- Interface to Siemens Teamcenter Manufacturing Resource Library (MRL)
- Integrated within the Siemens CNC Shopfloor Management Software Suite and Siemens SINUMERIK Integrate for Production technology portfolios
Benefits of Siemens SINUMERIK Manage MyResources / Tools
- Increase tool visibility on the shop floor throughout production
- Reduce physical tool inventory and costs
- Minimize tool shortages and machine downtimes
- Maximize tool lifetime
- Create a single source of tool data across the enterprise
- Increase efficiency in shop floor and data management processes
- Improve quality of tool data
- Facilitate change management and collaboration
Engineering’s Expertise
The right solution is critical to creating and managing an efficient shop floor environment. Siemens SINUMERIK Manage MyResources / Tools increases the capabilities and value of your central manufacturing database by extending it to cover the physical tools and resources in your production plant. This single source of information leads to numerous operational and business benefits for the enterprise. Manage MyResources / Tools digitalizes tool management, enables personnel to effectively manage and build physical tool assemblies based on the latest released tooling information and allows for the full traceability of physical tools on the shop floor. Procurement and planning can minimize tool inventory, but also act proactively to ensure that tools will be in stock when they are needed. Tool managers can execute tool balancing and ensure that they have the right tools to complete the job. Engineering has been working with CNC machining and manufacturing customers of all shapes and sizes for over a decade in order to help them successfully choose and implement solutions like Siemens SINUMERIK Manage MyResources / Tools in order to digitalize data management, optimize processes and achieve the highest level of efficiency on the shop floor.
Interested in speaking to one of our experts? Contact us at [email protected].
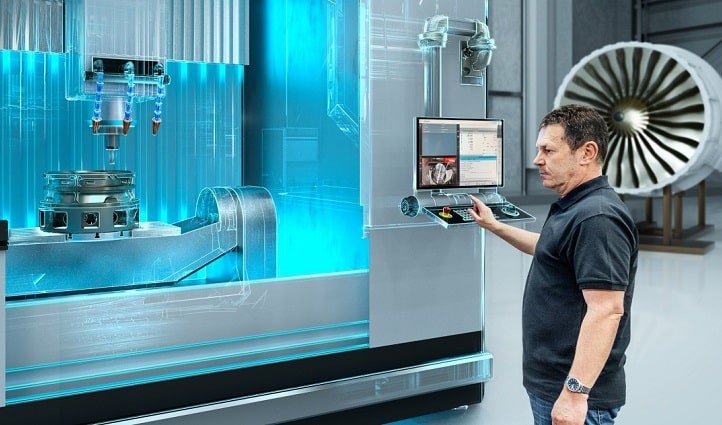