sedApta Software Suite
About sedApta Software Suite
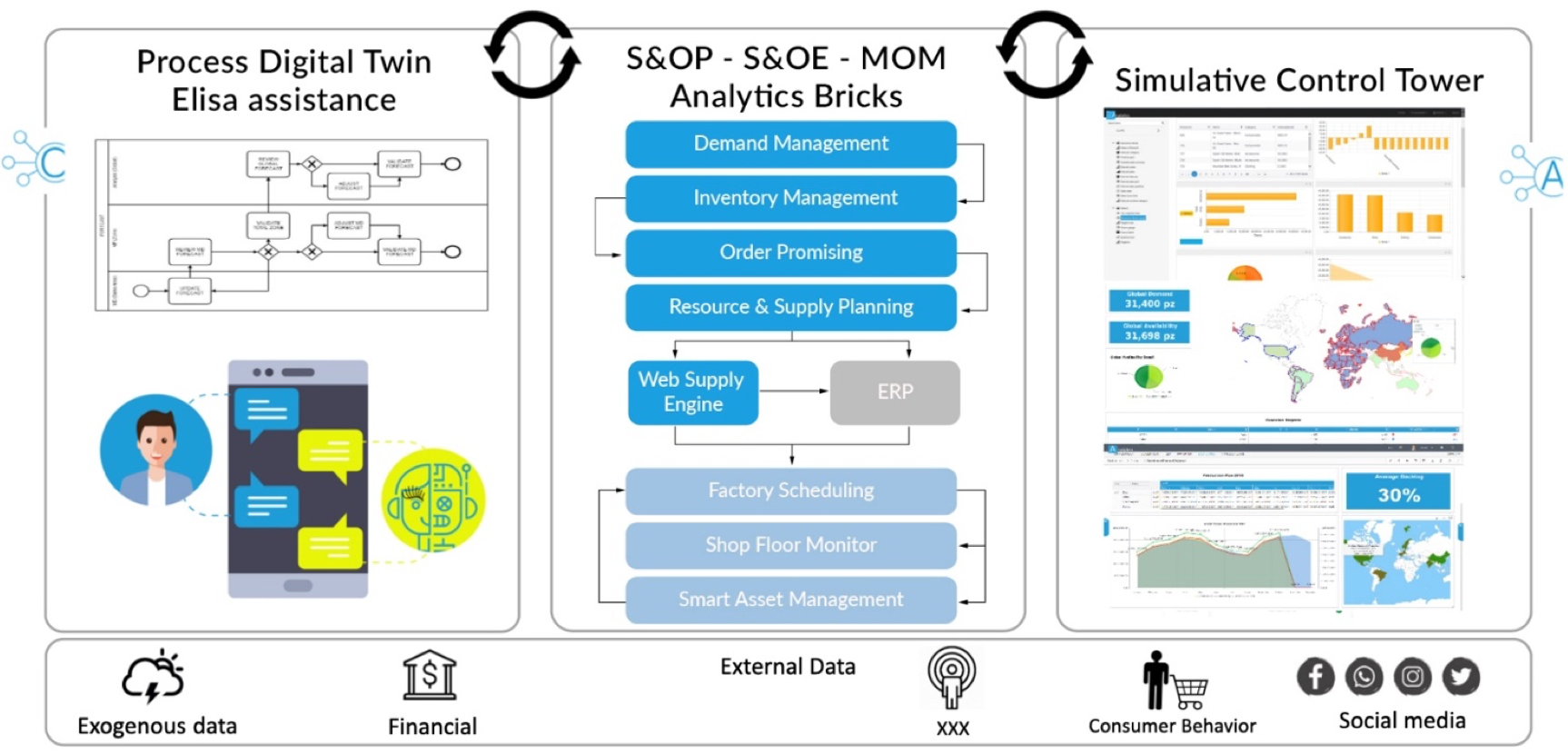
The sedApta Software Suite is an innovative technology platform comprised of integrated solutions that support industrial organizations in meeting their planning and execution needs in all functions of Supply Chain Management, thus maximizing business profitability and facilitating collaboration among different departments and plants across the enterprise. Thanks to the modularity of its orchestrated components and their ability to work together, both among one another as well as with third-party software solutions, the sedApta Software Suite enables companies to transform and optimize all processes along their supply chain.
The modules of the sedApta Software Suite cover:
- Sales & Operations Planning (S&OP);
- Sales & Operations Execution (S&OE);
- Manufacturing Operations Management (MOM).
sedApta Analytics Bricks
The sedApta Software Suite’s Analytics Bricks align your enterprise planning activities – in terms of sales, manufacturing and supply chain – with real factory resource and asset availability, thus enabling your company to optimize processes and become more responsive to unexpected changes.
Demand Management
The Demand Management module ensures the achievement of important strategical advantages by optimizing your demand analysis and demand forecasting activities.
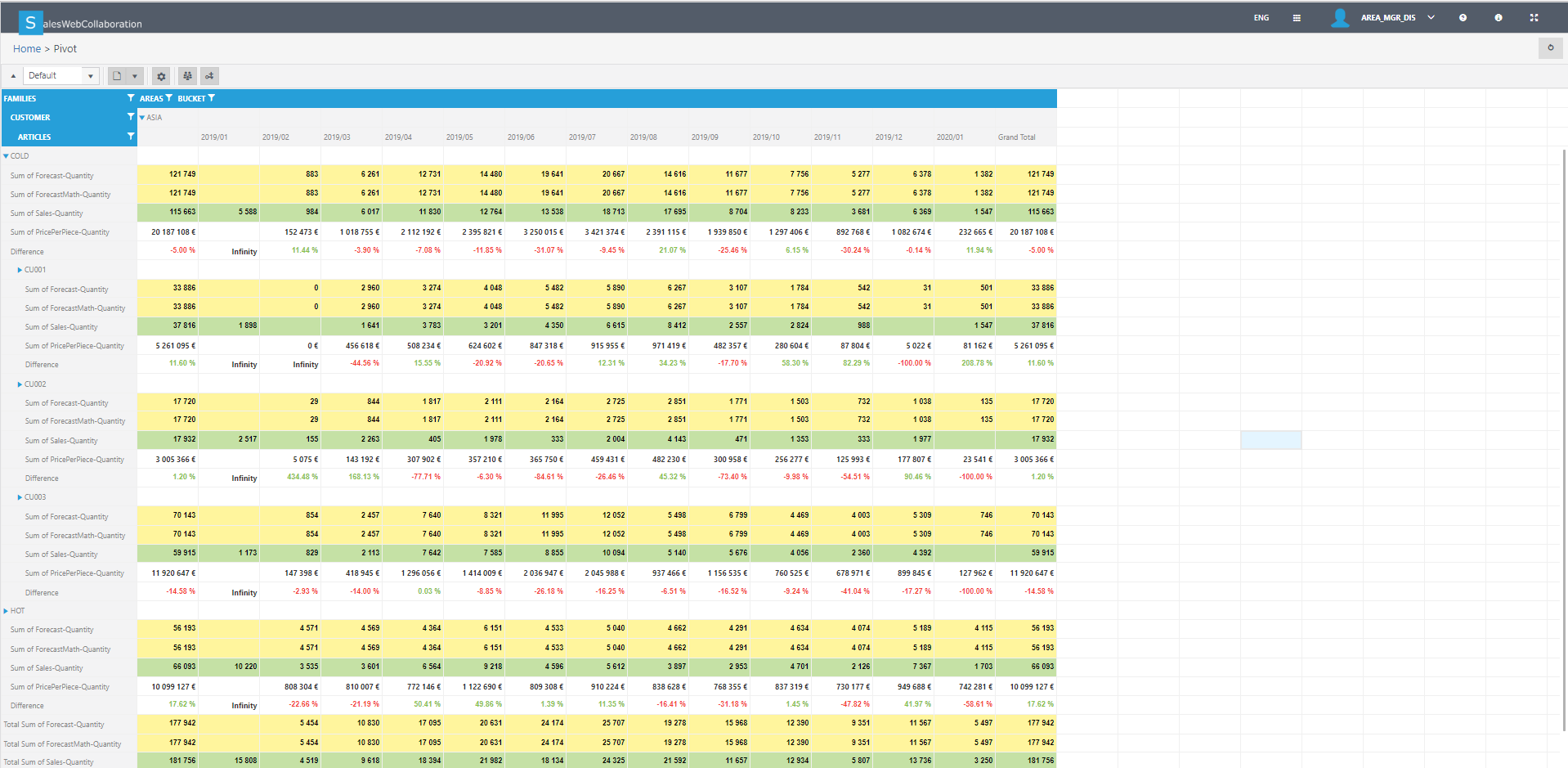
- Statistical Sales Forecasting: aggregate input from your sales and marketing teams with historical sales data to produce an accurate demand forecast consensus.
- Sales Planning: perform manual forcing actions on sales forecast data at different aggregation levels.
- Collaborative Sales Forecasting: simulate scenarios to predict demand and achieve collaborative generation of sales forecast adapted to your company’s unique organizational structure.
Inventory Management
The Inventory Management module helps you automatically generate and optimize inventory plans based on inputs and constraints from relevant nodes across your logistical supply chain network.
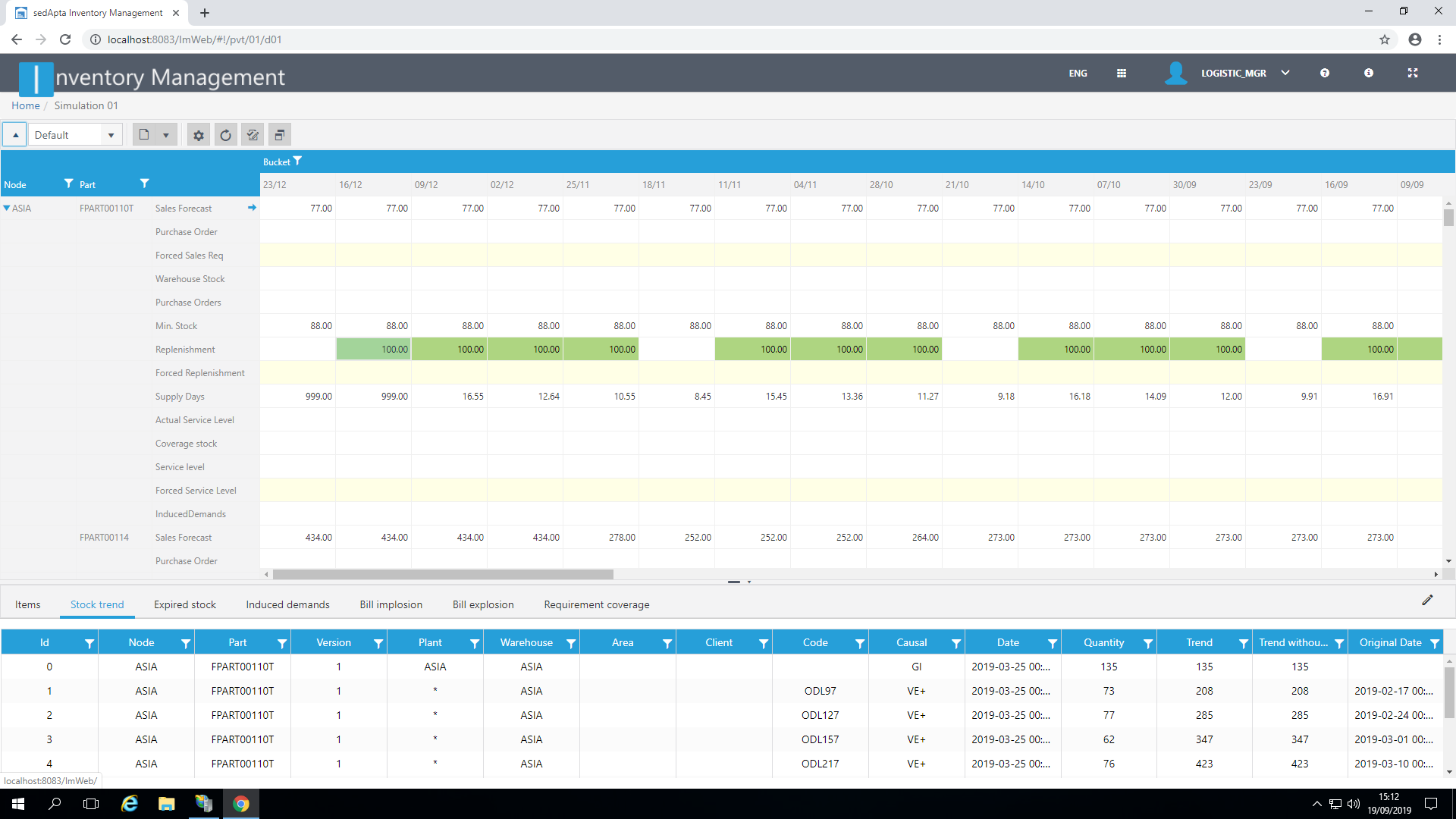
- Inventory Control: simulate scenarios to create a stock replenishment plan based on your sales forecast, target service levels, current stock levels, budget and existing customer orders.
- Inventory Optimization: calculate your optimal safety stock levels taking desired customer service levels, forecast reliability, financial and logistical constraints into account.
Order Promising
Taking warehouse availability and your master production plan into account, the Order Promising module provides a single consolidated view of supply and demand to enable reliable, real-time delivery commitments.
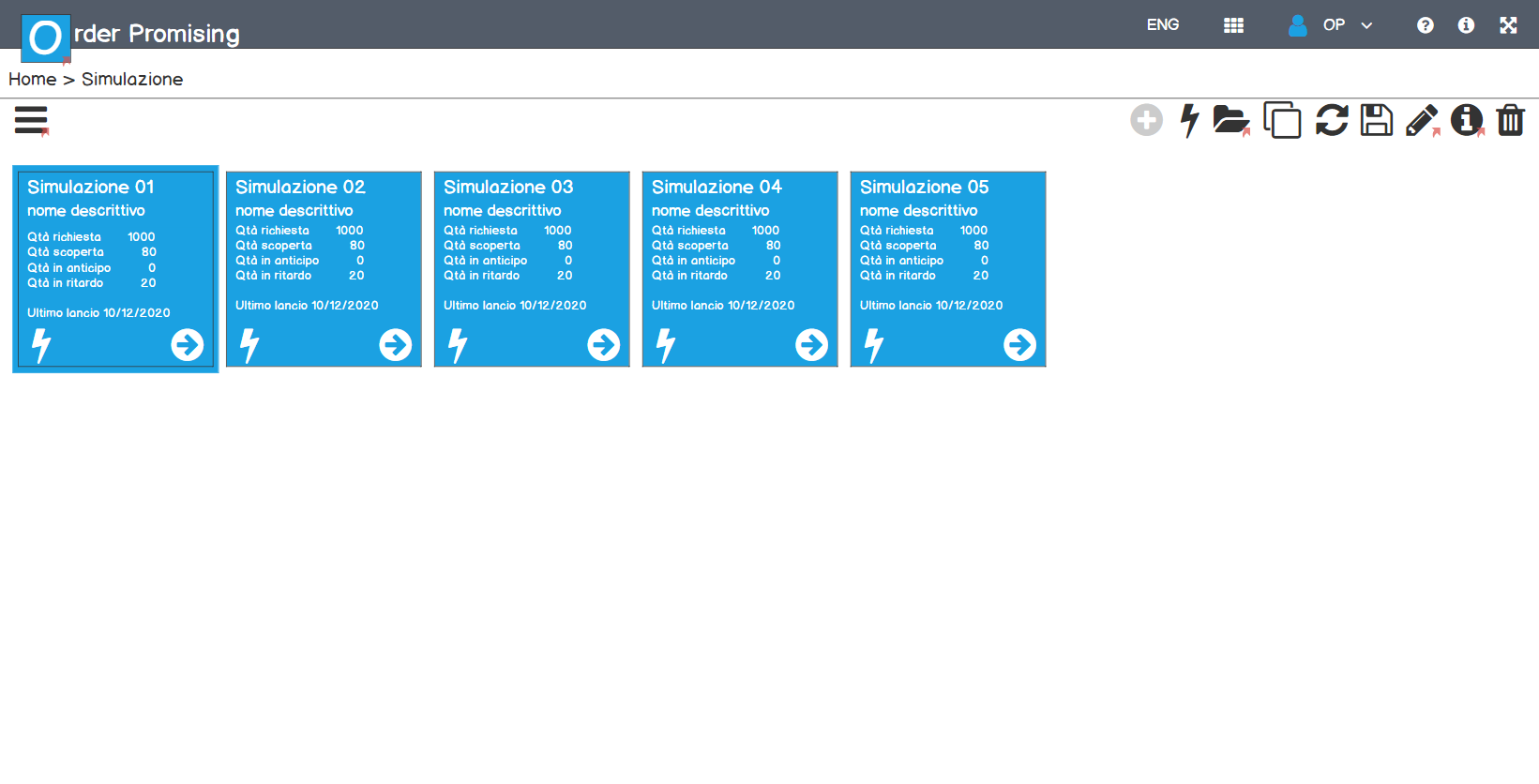
- Customer Order Fulfillment: confirm customer delivery dates via simulations driven by service-level assignment criteria and heuristics that verify inventory and incoming plans from both the production and supply sides.
- Heuristics Management: define and formulate customer order sorting rules taking required delivery dates, status, priority, penalty existence and transportation constraints into account.
- Interactive Forcing: execute manual order fulfillment (partial, split or total) and manual override of automated order allocation outcomes.
Resource & Supply Planning
The Resource & Supply Planning module reconciles physical, logistical, financial and production constraints to validate your demand forecast against the actual capacity of resources within your supply chain network.
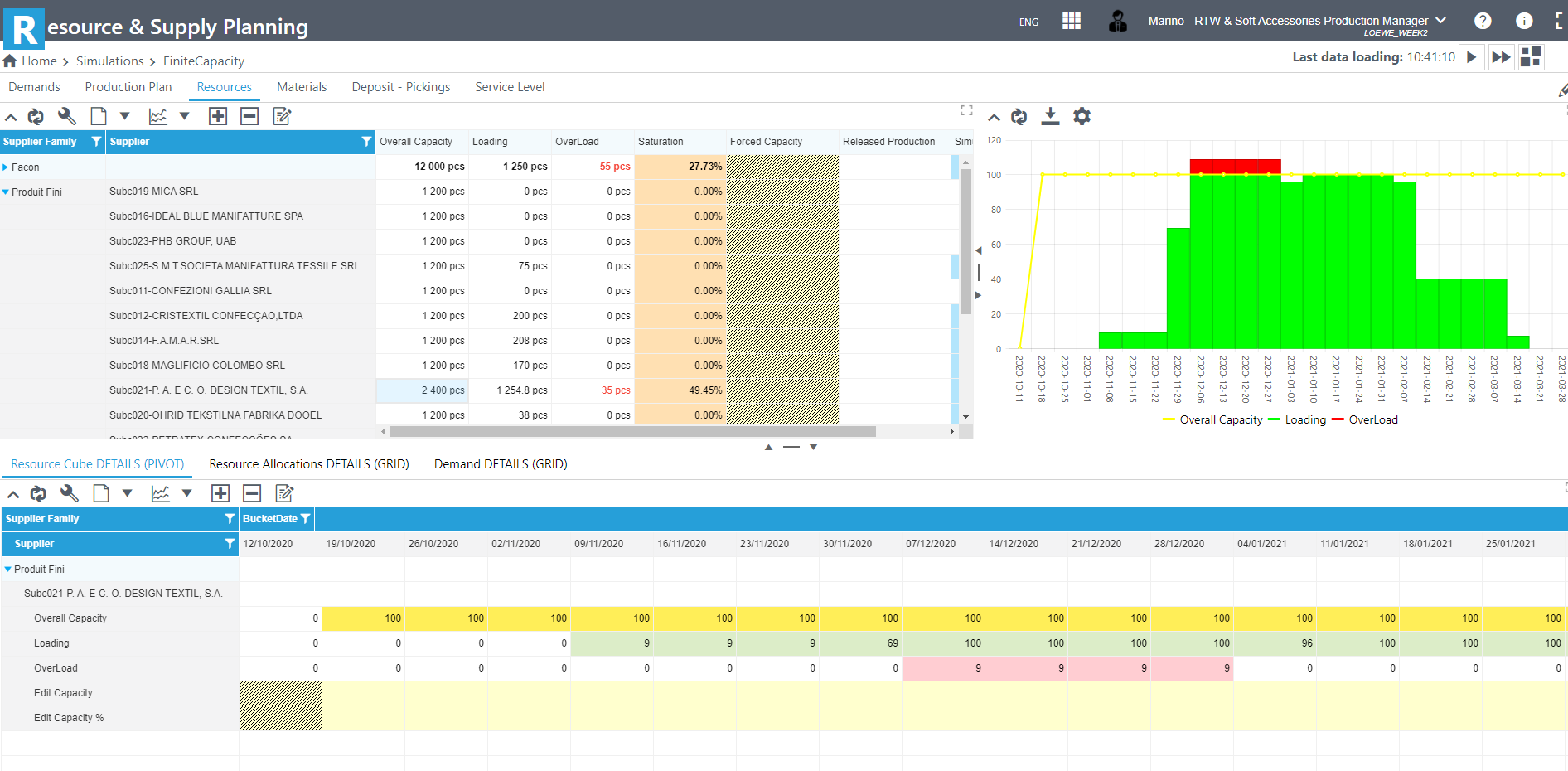
- Cross-Plant Capacity Planning: starting from an item-based or demand-based priority, dynamically assign orders to different plants, comparing the required capacity to cover demands and the available capacity of each site.
- Rough-Cut Capacity Planning: validate your demand forecast through strategic and/or long-term planning calculated at the aggregate level, both in terms of resources and product families.
- Detailed Capacity Planning: validate your demand forecast through the evaluation of the actual capacity and availability of the necessary physical, logistical and economic resources.
- Integrated Planning: leverage a unified data model to evaluate and predict different product mix scenarios, with access to inventory and capacity realignment capabilities within a highly-integrated synergistic process.
Web Supply Engine
The Web Supply Engine module facilitates alignment with external contractors and different suppliers by providing a unified digital environment for collaboration.
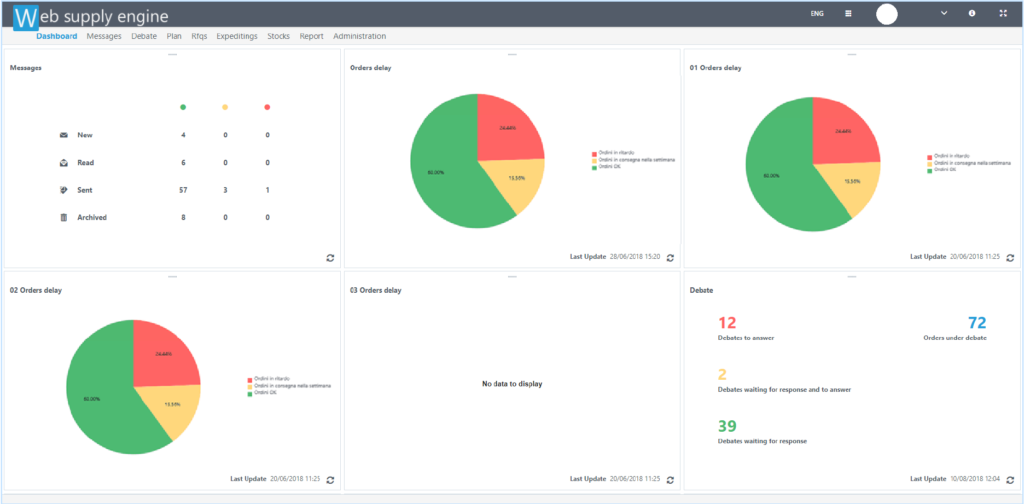
- Work Plan Collaboration: share short-term and/or medium-term plans with relevant external players, particularly contractors and suppliers.
- Supplier Debating: utilize a single virtual environment to discuss and share plan details with suppliers in order to ensure consensus on shipping dates, quantities to be delivered, price conditions, etc.
- Supplier Notification Management: continuously monitor production statuses on the supplier side and send automatic notifications regarding inspection calendars and quality control plans.
Factory Scheduling
Taking order priorities, lead times, set-up times and other plant-specific constraints into account, the Factory Scheduling module helps manage and optimize the short-term scheduling of production resources and capacities.
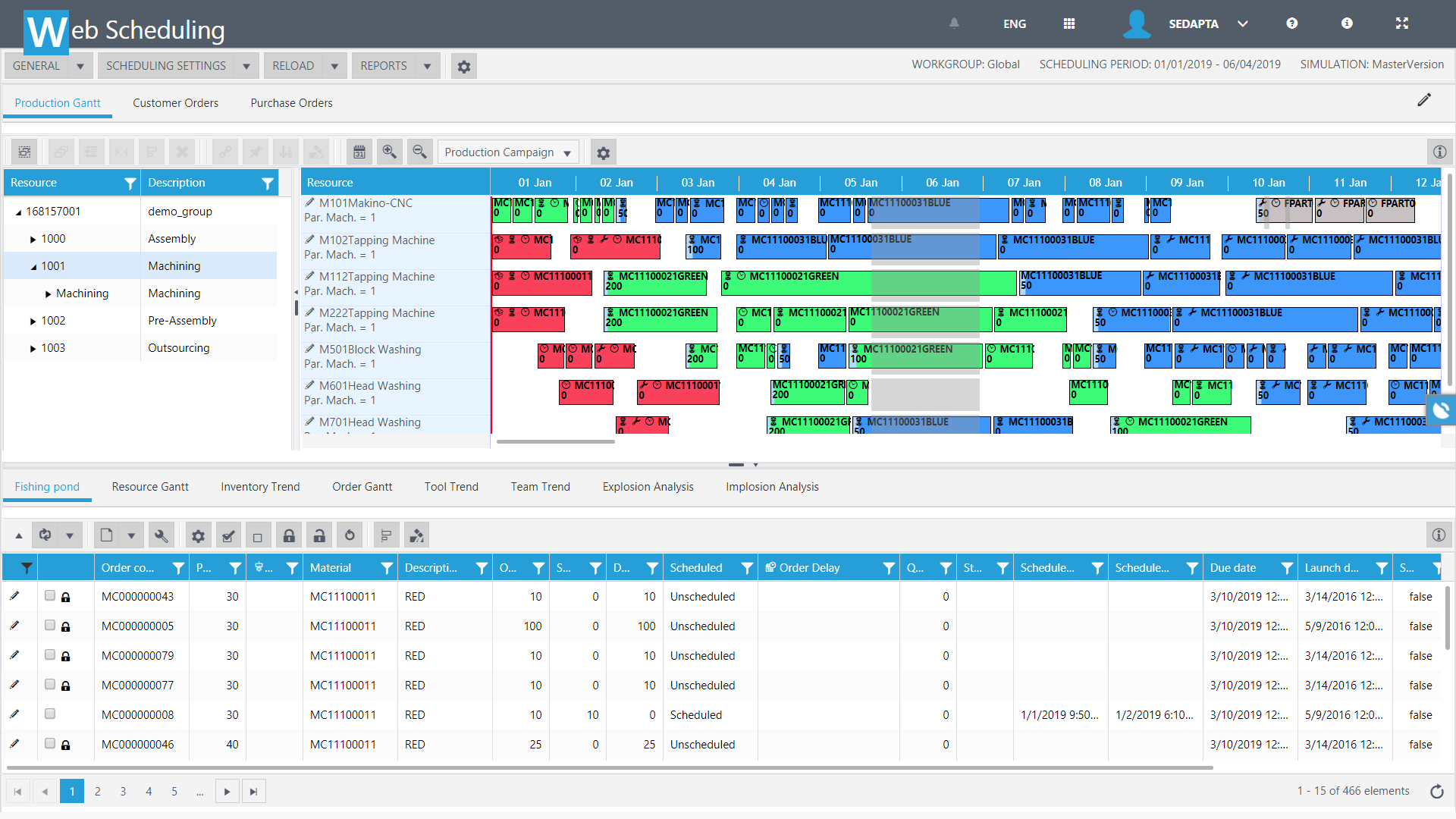
- Finite Capacity Scheduling: create and manage your plant's production schedule by balancing medium/long-term production objectives with short-term operative needs.
- Production Sequence Optimization: dynamically allocate orders according to pre-configured rules, optimizing production sequences, reducing plant set-up times and speeding up time-to-market.
- Material Management: manage incoming raw materials needed for your production process, synchronizing production plans, quality control and material handling.
- Multi-Scenario Simulation and Analysis: simulate and benchmark alternative production scenarios with related Key Performance Indicators (KPIs), "what if” analyses and change propagation.
Shop Floor Monitor
The Shop Floor Monitor module collects and aggregates data throughout your manufacturing process, enabling real-time visibility into production and better decision-making in response to unexpected changes or interruptions.
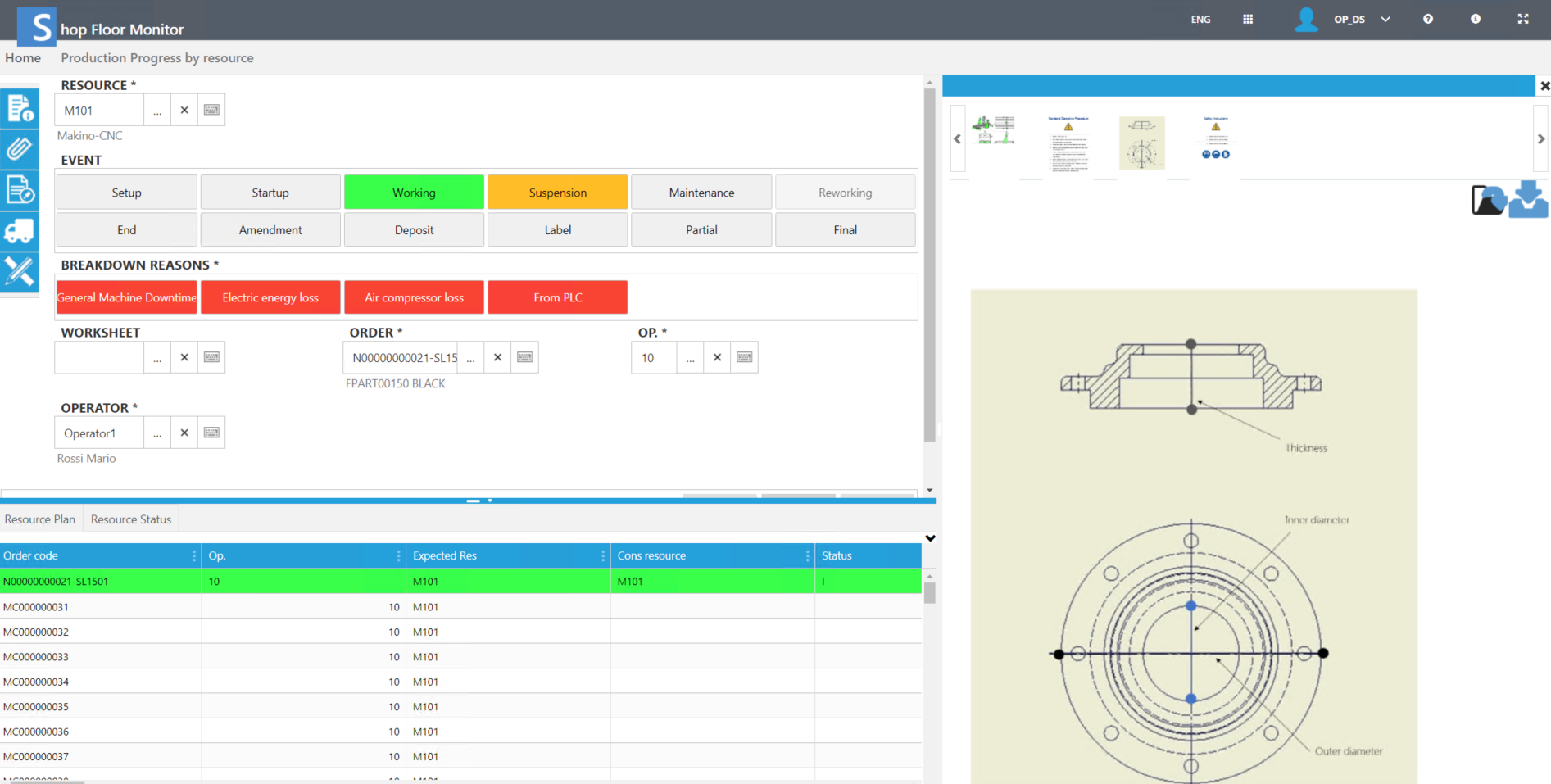
- Shop Floor Monitoring & Control: access a complete real-time panorama view of events, assets, processes and statuses throughout your production process and from any web-enabled device or industrial terminal.
- Performance Analytics & OEE: study your performance analytics via dashboards displaying configurable KPIs such as Manufacturing Quality, Production Productivity, Asset Availability and Overall Equipment Effectiveness.
- Event & Alarm Management: enable automated alarms to alert relevant department supervisors, such as quality, maintenance or material-handling personnel, in case of production issues, changes and/or downtimes.
Smart Asset Management
The Smart Asset Management module enables the automatic detection and correction of production asset failures, both before they occur and before they are able to generate serious product defects.
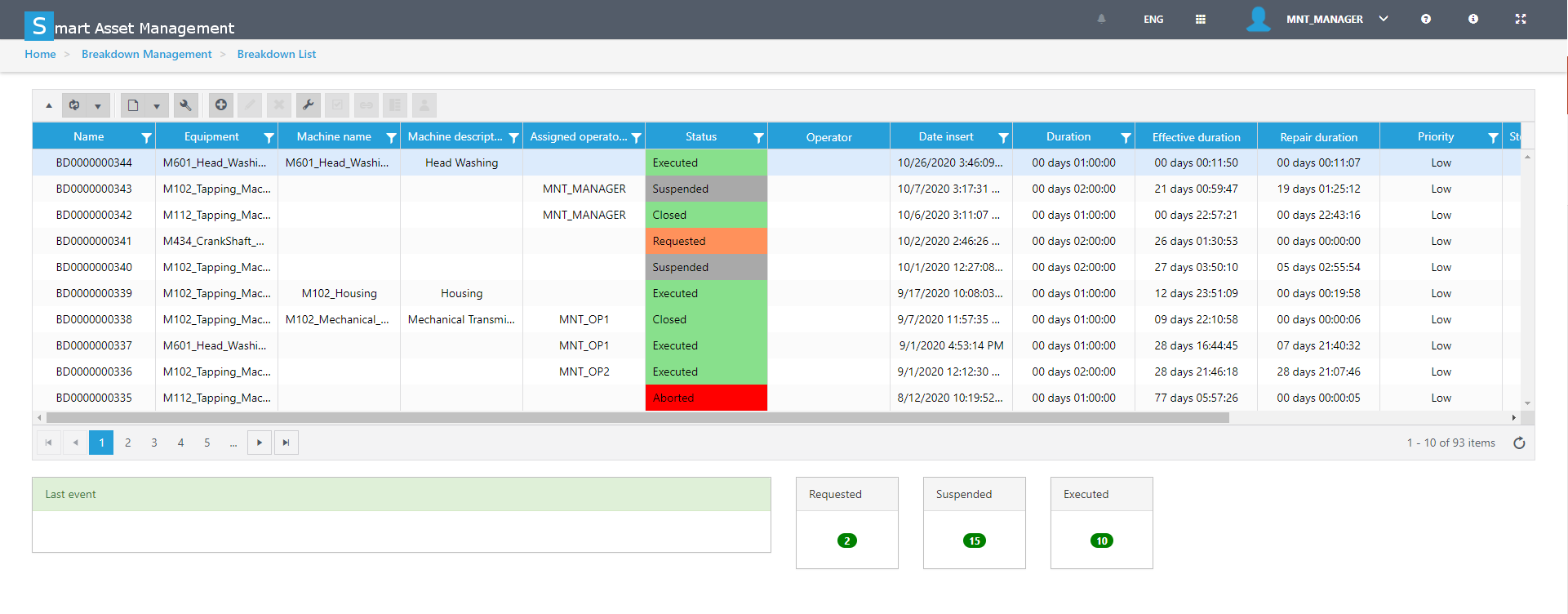
- Routine Asset Maintenance: enable autonomous execution of routine maintenance on plant assets and machines based on pre-defined rules.
- Programmed Asset Maintenance: inspect and correct incipient asset failures, either before they occur or before they turn into major defects and downtimes.
- Condition-Based Asset Maintenance: monitor asset measurements (noise, vibrations, temperature, pressure, machine cycles, etc.), automatically triggering a maintenance task when pre-defined constraints are violated.
- Corrective Asset Maintenance: create and assign maintenance tasks after a failure is detected in order to restore an asset to a functional/operative condition.
- Asset Error Analysis & Reporting: generate performance reports, study asset trends and run defect analyses, driving continuous improvement in your asset performance and management strategies.
sedApta Simulative Control Tower
The sedApta Simulative Control Tower is a software tool designed to improve supply chain visibility and responsiveness. The Simulative Control Tower’s modeling approach enables you to compare and analyze a number of different supply chain scenarios, to quantify the resulting impacts of different changes on business and operational goals, and to enable more effective and rapid decision-making at the management level. The Simulative Control Tower also drives structured alignment among all the relevant players across your supply chain network, continuously driven and supported by contextual information and its online collaboration capabilities.
sedApta Digital Twin & Elisa Assistance
Thanks to a strategic partnership with Elisa, a leading provider of Artificial Intelligence services and solutions, combined with the process orchestration approach around which the sedApta product portfolio was built, the sedApta offering can be implemented with state-of-the-art 3D visualization, Machine Learning and analytical capabilities running in the background. As a result, the sedApta Software Suite is not only able to drive automation and optimization across all of your business and operational planning processes, but it can help identify, predict and prevent inefficiencies by transforming your data into actionable insights at each phase of your value chain, too.
Benefits of sedApta Software Suite
- Optimize supply chain planning and execution
- Improve demand forecast accuracy
- Increase order promising reliability
- Decrease inventory levels and costs
- Improve customer service levels
- Increase business process efficiency
- Increase operational productivity
- Ensure supply chain visibility and orchestration
Engineering’s Expertise
Today, the sedApta Software Suite is being leveraged by over 1000 customers across a number of different manufacturing and industrial sectors worldwide in order to help them coordinate and synchronize their supply chain processes and stakeholders, while simultaneously aligning production planning (S&OP), production scheduling (S&OE) and production execution (MOM). Engineering is the sedApta Group’s preferred system integrator and implementation partner for North America. The sedApta Software Suite, together with our extensive expertise in Industry 4.0 and Sales & Operations Planning processes, is the right combination for companies embarking on a challenging supply chain optimization and standardization journey.
Interested in speaking to one of our experts? Contact us at [email protected].
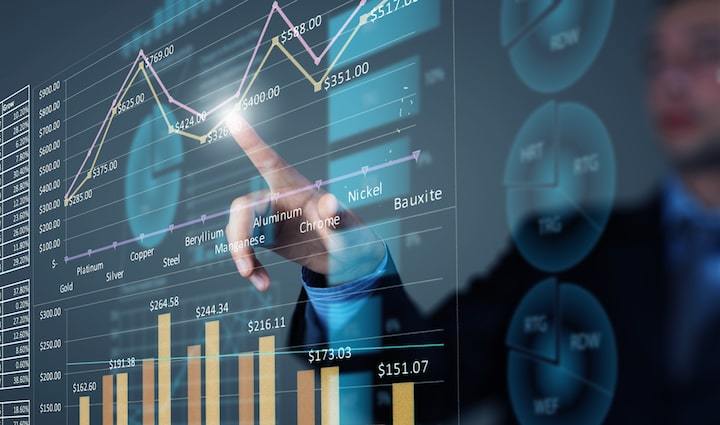